Dual graphing method
A dual patterning and patterning technology, which is applied in the direction of photoplate making process, optics, and optomechanical equipment on the pattern surface, can solve the problem of low patterning precision, improve integration, improve precision, and reduce pattern lines. wide effect
- Summary
- Abstract
- Description
- Claims
- Application Information
AI Technical Summary
Problems solved by technology
Method used
Image
Examples
Embodiment Construction
[0036] The double patterning method of the prior art divides the exposure pattern into two independent patterns with low density, and then exposes them separately. Due to the limitation of the exposure process, the patterning accuracy is still low, which cannot meet the needs of further processes.
[0037] In the double patterning method of the technical solution, the hard mask layer is first imprinted using an imprint mold, the first pattern is transferred to the hard mask layer, and then photoresist is formed on the hard mask layer layer, and pattern the photoresist layer, define a second pattern on the second photoresist, then use the patterned photoresist layer as a mask to etch the hard mask layer, and The second pattern is transferred to the hard mask layer. Using an imprinting mold for imprinting can get rid of the limitation of exposure process during lithography, which is beneficial to improve the precision of patterning, reduce the line width of patterns, and improve...
PUM
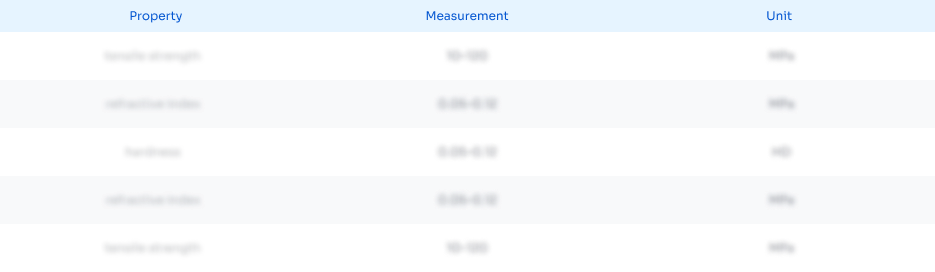
Abstract
Description
Claims
Application Information

- R&D
- Intellectual Property
- Life Sciences
- Materials
- Tech Scout
- Unparalleled Data Quality
- Higher Quality Content
- 60% Fewer Hallucinations
Browse by: Latest US Patents, China's latest patents, Technical Efficacy Thesaurus, Application Domain, Technology Topic, Popular Technical Reports.
© 2025 PatSnap. All rights reserved.Legal|Privacy policy|Modern Slavery Act Transparency Statement|Sitemap|About US| Contact US: help@patsnap.com