Composition capable of greatly improving crude oil recovery efficiency and preparation method thereof
A composition and recovery technology, applied in the field of composition and its preparation that can greatly increase oil recovery, can solve problems such as fouling damage, high use concentration, and alkali corrosion in ASP flooding, and achieve The ability to reduce interfacial tension, good technical effect, and the effect of enhancing oil recovery
- Summary
- Abstract
- Description
- Claims
- Application Information
AI Technical Summary
Problems solved by technology
Method used
Image
Examples
Embodiment 1
[0031](1) Add 93g (0.5 mole) dodecyl alcohol and the calcium oxide catalyst of alcohol weight 1% in the reactor that condensing device, stirring device and gas disperser are housed, when heating to 135 ℃ while flowing nitrogen, add 8 grams water, stirred for 1 hour. Then first distilled water at normal pressure, then decompressed under 20 mm Hg vacuum, evaporated moisture at 140 DEG C in vacuum for 20 minutes, cooled the solution to 80 DEG C, slowly added dropwise neutralizing catalyst theoretical acid amount of 20% by weight concentrated sulfuric acid. Heat the system temperature to 80-90°C, turn on the vacuum system, dehydrate under high vacuum for 1 hour, then use nitrogen to blow 3-4 times to remove the air in the system, then adjust the reaction temperature of the system to 150°C Enter 70g oxirane, control pressure<0.60MPa and carry out alkoxylation reaction; After the reaction finishes, purging system with nitrogen, removes unreacted oxirane, after cooling, neutralize, ...
Embodiment 2
[0037] (1) Add the calcium oxide catalyst of 135g (0.5 mole) stearyl alcohol and alcohol weight 1% in the reactor that condensing device, stirring device and gas disperser are housed, when heating to 135 ℃ while flowing nitrogen, add 10g water , and stirred for 1 hour. Then first distilled water at normal pressure, then decompressed under 20 mm Hg vacuum, evaporated moisture at 140 DEG C in vacuum for 20 minutes, cooled the solution to 80 DEG C, slowly added dropwise neutralizing catalyst theoretical acid amount of 20% by weight concentrated sulfuric acid. Heat the system temperature to 80-90°C, turn on the vacuum system, dehydrate under high vacuum for 1 hour, then use nitrogen to blow 3-4 times to remove the air in the system, then adjust the reaction temperature of the system to 150°C Enter 155g oxirane, control pressure<0.60MPa and carry out alkoxylation reaction; After the reaction finishes, purging system with nitrogen gas, removes unreacted oxirane, after cooling, neut...
Embodiment 3
[0043] (1) add the calcium oxide catalyst of 94g (0.5 moles) coconut oil alcohol and alcohol weight 1% in the reactor that condensing unit, agitator and gas disperser are housed, when heating to 135 ℃ while logical nitrogen, add 8g water , and stirred for 1 hour. Then first distilled water at normal pressure, then decompressed under 20 mm Hg vacuum, evaporated moisture at 140 DEG C in vacuum for 20 minutes, cooled the solution to 80 DEG C, slowly added dropwise neutralizing catalyst theoretical acid amount of 20% by weight concentrated sulfuric acid. Heat the system temperature to 80-90°C, turn on the vacuum system, dehydrate under high vacuum for 1 hour, then use nitrogen to blow 3-4 times to remove the air in the system, then adjust the reaction temperature of the system to 150°C Enter 155g oxirane, control pressure<0.60MPa and carry out alkoxylation reaction; After the reaction finishes, purging system with nitrogen gas, removes unreacted oxirane, after cooling, neutralize...
PUM
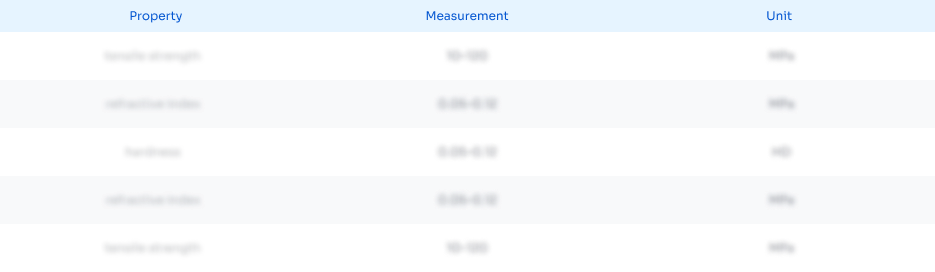
Abstract
Description
Claims
Application Information

- R&D
- Intellectual Property
- Life Sciences
- Materials
- Tech Scout
- Unparalleled Data Quality
- Higher Quality Content
- 60% Fewer Hallucinations
Browse by: Latest US Patents, China's latest patents, Technical Efficacy Thesaurus, Application Domain, Technology Topic, Popular Technical Reports.
© 2025 PatSnap. All rights reserved.Legal|Privacy policy|Modern Slavery Act Transparency Statement|Sitemap|About US| Contact US: help@patsnap.com