Preparation method of nickel-based hydrogenation catalyst
A hydrogenation catalyst and nickel-based technology, applied in the field of preparation of nickel-based hydrogenation catalysts, can solve the problems of high precipitation temperature, particularly demanding sulfur content, affecting the activity level of nickel, etc., and achieve the effect of uniform precipitation environment
- Summary
- Abstract
- Description
- Claims
- Application Information
AI Technical Summary
Problems solved by technology
Method used
Image
Examples
Embodiment 1
[0029] 279.5g of nickel chloride hexahydrate and 11.0g of lanthanum nitrate hexahydrate are formulated into a mixed solution so that the concentration of the two salts in this solution is 0.6mol / L. After the two salts are all dissolved, add pseudoboehmite (containing Al 2 o 3 70% (mass fraction)) 92.9g, make slurry stand-by; Dissolve 318g sodium carbonate in water, be mixed with the precipitating agent solution that concentration is 1.0mol / L, stand-by; Add 1000mL clean water in 8000mL reactor , heat and turn on the stirring equipment. When the temperature rises to 80°C, keep the temperature in the kettle, start to add the mixed slurry and alkaline precipitant solution in parallel, and control the flow rate of the mixed slurry to 40mL / min and the flow rate of the alkaline precipitant solution to 55mL / min, keep the pH value of the slurry in the reactor at 7.2, when all the acidic mixed slurry is added, use the alkaline precipitant solution to adjust the pH value of the slurry ...
Embodiment 2
[0031] The preparation process is the same as in Example 1, except that the concentration of the two salts in the solution is changed to 0.3mol / L, the concentration of the precipitant solution is changed to 1.5mol / L, and the prepared nickel-based hydrogenation catalyst is C 2 , and the analysis results are shown in Table 1.
Embodiment 3
[0033] The preparation process is the same as in Example 1, and 1500mL of clean water is pre-added in the 8000mL reactor, and the prepared nickel-based hydrogenation catalyst C 3 , and the analysis results are shown in Table 1.
PUM
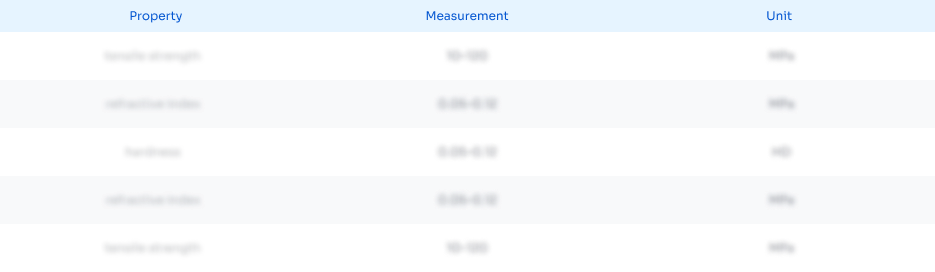
Abstract
Description
Claims
Application Information

- R&D Engineer
- R&D Manager
- IP Professional
- Industry Leading Data Capabilities
- Powerful AI technology
- Patent DNA Extraction
Browse by: Latest US Patents, China's latest patents, Technical Efficacy Thesaurus, Application Domain, Technology Topic, Popular Technical Reports.
© 2024 PatSnap. All rights reserved.Legal|Privacy policy|Modern Slavery Act Transparency Statement|Sitemap|About US| Contact US: help@patsnap.com