Polysiloxane polymer and preparation method thereof
A technology of polysiloxane and polymer, applied in the field of polysiloxane polymer and its preparation, can solve problems such as difficult removal, increase product viscosity, reduce storage stability, etc., achieve less side reactions, simple reaction, low The effect of viscosity
- Summary
- Abstract
- Description
- Claims
- Application Information
AI Technical Summary
Problems solved by technology
Method used
Image
Examples
Embodiment 1
[0023] Embodiment 1, the preparation of polysiloxane polymer
[0024]In a 250mL three-necked flask, add 96.2g of monomeric methylhydrogensiloxane cyclic body, 34.5g of methylvinylcyclotetrasiloxane and 1.87g of tetramethyldivinyldisiloxane (the In the reaction system, the molar ratio of methyl hydrogen siloxane ring body and methyl vinyl cyclotetrasiloxane is 1:4; The molar ratio of alkane ring body and the total amount of monomer units of methyl vinyl cyclotetrasiloxane is 1:100); under magnetic stirring, add 0.39g CF 3 SO 3 H (which accounts for 0.3% of the total mass of the methylhydrogensiloxane ring body and the methylvinylcyclotetrasiloxane siloxane monomer) and 0.015g deionized water, stirred and reacted for 3 hours in an oil bath at 65°C Viscosity After there is no obvious change, after feeding sufficient amount of ammonia gas, the low boiling matter is removed under vacuum at 140-150°C; after filtering through a G3 sand core funnel, 115g of colorless transparent liq...
Embodiment 2
[0025] Embodiment 2, the preparation of polysiloxane polymer
[0026] In a 1000mL three-necked flask, add 451g methylhydrogensiloxane ring body, 215g methylvinylcyclotetrasiloxane and 4.66g end-capping agent tetramethyldivinyldisiloxane (in this reaction system, The molar ratio of methyl hydrogen siloxane ring body and methyl vinyl cyclotetrasiloxane is 3:1; The molar ratio of the total substance amount of base vinyl cyclotetrasiloxane is 0.5:100); under magnetic stirring, add 0.78g CF 3 SO 3 H (which accounts for 0.1% of the total mass of the siloxane monomer of the methyl hydrogen siloxane ring body and the methyl vinyl cyclotetrasiloxane), stirred and reacted for 4 hours in an oil bath at 65° C., and introduced a sufficient amount of ammonia After degassing, remove the low boiler under vacuum under reduced pressure at 140-150°C; after filtering through a G3 sand core funnel, obtain 143g colorless transparent liquid (yield 89%), as shown in formula (I), wherein, x is 0.75...
Embodiment 3
[0027] Embodiment 3, the preparation of polysiloxane polymer
[0028] In a 1000mL three-necked flask, add 361g methylhydrogensiloxane ring body, 433g methylvinylcyclotetrasiloxane and 1.87g end-capping agent tetramethyldivinyldisiloxane (in this reaction system, The molar ratio of methyl hydrogen siloxane ring body and methyl vinyl cyclotetrasiloxane is 1.2:1; The molar ratio of the total substance amount of base vinyl cyclotetrasiloxane is 0.2:100); under magnetic stirring, add 0.86g CF 3 SO 3 H (which accounts for 0.11% of the total mass of siloxane monomers of methylhydrogensiloxane ring body and methylvinyl cyclotetrasiloxane) and 0.086 deionized water, stirred and reacted at 65°C in an oil bath for 4 hours, After feeding a sufficient amount of ammonia, remove the low boilers under vacuum at 140-150° C., and filter through a G3 sand core funnel to obtain 590 g of a colorless transparent liquid (yield 75%), as shown in formula (I) , wherein, x is 0.55, y is 0.45, z is 0,...
PUM
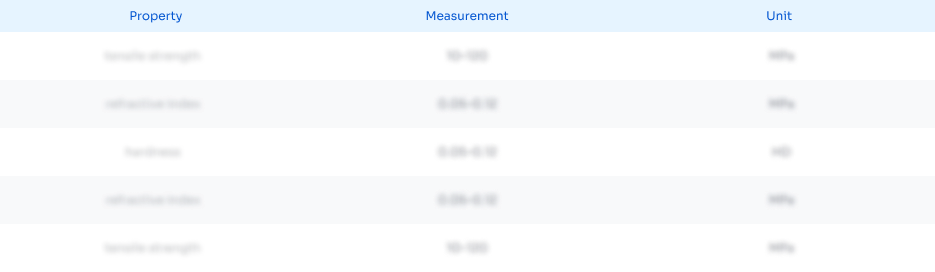
Abstract
Description
Claims
Application Information

- Generate Ideas
- Intellectual Property
- Life Sciences
- Materials
- Tech Scout
- Unparalleled Data Quality
- Higher Quality Content
- 60% Fewer Hallucinations
Browse by: Latest US Patents, China's latest patents, Technical Efficacy Thesaurus, Application Domain, Technology Topic, Popular Technical Reports.
© 2025 PatSnap. All rights reserved.Legal|Privacy policy|Modern Slavery Act Transparency Statement|Sitemap|About US| Contact US: help@patsnap.com