Integrated cantilever rotor structure
A cantilever rotor and one-piece technology, applied in the direction of blade support components, jet propulsion devices, engine components, etc., can solve the problems of complex mechanical structure, low reliability, power consumption and other problems of the unit, and achieve shortened cantilever length, reliable use, Effect of reducing vibration amplitude
- Summary
- Abstract
- Description
- Claims
- Application Information
AI Technical Summary
Problems solved by technology
Method used
Image
Examples
Embodiment Construction
[0008] As shown in the figure, the integrated cantilever rotor structure includes generator rotor 2, centrifugal compressor impeller 4, sealing grate teeth 5, and radial turbine impeller 6 arranged in sequence on the center tie rod 3. The centrifugal compressor impeller 4 One side of the centrifugal compressor impeller 4 and the radial turbine impeller 6 are connected back to back through the sealed grate teeth 5 and the radial turbine impeller 6 in the manner of end face matching, and the other end of the centrifugal compressor impeller 4 is connected to the power generation The central tie rod 3 runs through the generator rotor 2, the centrifugal compressor impeller 4, the sealing grate 5 and the radial turbine impeller 6, and one end is provided with a boss and connected to the inner hole of the radial turbine impeller 6. Step fit, the other end is provided with threads and fixed by the lock nut 1, and the two sides of the generator rotor are respectively provided with suppo...
PUM
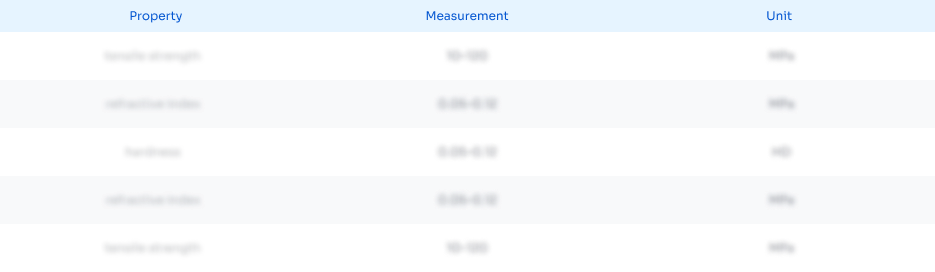
Abstract
Description
Claims
Application Information

- R&D
- Intellectual Property
- Life Sciences
- Materials
- Tech Scout
- Unparalleled Data Quality
- Higher Quality Content
- 60% Fewer Hallucinations
Browse by: Latest US Patents, China's latest patents, Technical Efficacy Thesaurus, Application Domain, Technology Topic, Popular Technical Reports.
© 2025 PatSnap. All rights reserved.Legal|Privacy policy|Modern Slavery Act Transparency Statement|Sitemap|About US| Contact US: help@patsnap.com