Ethylene vinyl acetate (EVA) adhesive film for solar cell and preparation method thereof
A technology of solar cells and adhesive films, applied in circuits, adhesives, photovoltaic power generation, etc., can solve problems such as backward quality and immature EVA film formula, and achieve improved adhesion, improved UV aging resistance, and improved humidity and heat aging. Effect
- Summary
- Abstract
- Description
- Claims
- Application Information
AI Technical Summary
Problems solved by technology
Method used
Image
Examples
Embodiment 1
[0035] In parts by mass, 1.0 parts of 1,1-bis(tert-butylperoxy)-3,3,5-trimethylcyclohexane, 0.2 parts of triallyl isocyanurate, 0.2 Parts of β(3,5-di-tert-butyl-4-hydroxyphenyl) octadecyl propionate, 0.2 parts of tris(2,4-di-tert-butylphenol) phosphite, 0.3 parts of ethyl- 2,2,6,6-Tetramethyl-4-hydroxypiperidine succinate, 0.2 parts of 2-(2'-hydroxy-3'-tert-butyl-5'-octyl propionate)-benzotri Azole, 0.2 part of γ-methacryloxypropyl trimethoxysilane, 0.5 part of maleic anhydride grafted EVA pellets (MAH≥1%) are mixed uniformly; Rock in the feed at 50°C for 4h. The mixture is sucked into the upper hopper of the extruder, the temperature of the extruder is controlled between 45-65°C, the temperature of the die is controlled between 70-90°C, and the mixture is cast, cooled, drawn and coiled to obtain the thickness 0.5mm EVA film C1.
Embodiment 2
[0037] In parts by mass, 1.5 parts of 1,1-bis(tert-butylperoxy)-3,3,5-trimethylcyclohexane, 0.2 part of triallyl isocyanurate, 0.2 Parts of β (3,5-di-tert-butyl-4-hydroxyphenyl) octadecyl propionate, 0.2 parts of three (2,4-di-tert-butylphenol) phosphite, 0.2 parts of poly{[ 6-[(1,1,3,3-tetramethylbutyl)-amino]1,3,5-triazine-2,4-diyl][(2,2,6,6-tetramethyl Piperidinyl)-imino]-1,6-hexanediyl-[(,2,6,6-tetramethylpiperidinyl)-imino}, 0.1 parts of 2-(2′- Hydroxy-3'-tert-butyl-5'-propionate octyl)-benzotriazole, 0.1 part of γ-methacryloxypropyl trimethoxysilane, 1.0 part of maleic anhydride grafted EVA pellets ( MAH≥1%) and mix well; add to 100 parts of EVA pellets with VA content of 33% and rock at 55°C for 4h. The mixture is sucked into the upper hopper of the extruder, the temperature of the extruder is controlled between 50-75°C, the temperature of the die is controlled between 85-100°C, and the mixture is cast, cooled, drawn and coiled to obtain the thickness 0.5mm EVA film C2...
Embodiment 3
[0039] In terms of parts by mass, 1.0 parts of o-tert-butyl-o-(2-ethylhexyl) monoperoxycarbonate, 0.2 parts of triallyl cyanurate, 0.2 parts of β(3,5- Di-tert-butyl-4-hydroxyphenyl) propionic acid, 0.2 parts of tris(2,4-di-tert-butylphenol) phosphite, 0.2 parts of ethyl-2,2,6,6-tetramethyl-4 -Hydroxypiperidine succinate, 0.1 part of 2-(2'-hydroxy-3'-tert-butyl-5'-octyl propionate)-benzotriazole, 0.2 part of γ-methacryloxypropyl Base trimethoxysilane, 0.5 parts of maleic anhydride grafted EVA pellets (MAH ≥ 1%) and mix well; add to 100 parts of EVA pellets with VA content of 33% and rock at 50°C for 4h. The mixture is sucked into the upper hopper of the extruder, the temperature of the extruder is controlled between 45-70°C, the temperature of the die is controlled between 85-100°C, and the mixture is cast, cooled, drawn and coiled to obtain the thickness 0.5mm EVA film C3.
PUM
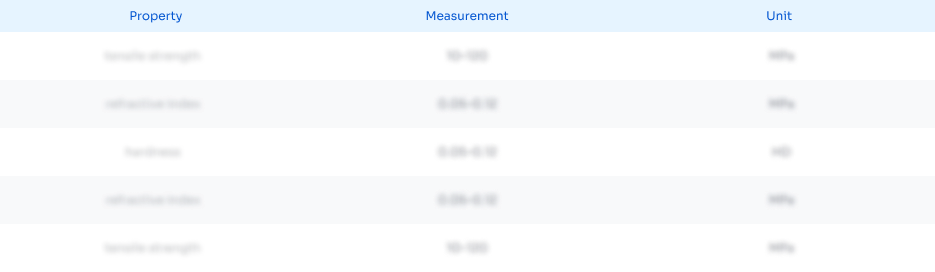
Abstract
Description
Claims
Application Information

- R&D Engineer
- R&D Manager
- IP Professional
- Industry Leading Data Capabilities
- Powerful AI technology
- Patent DNA Extraction
Browse by: Latest US Patents, China's latest patents, Technical Efficacy Thesaurus, Application Domain, Technology Topic, Popular Technical Reports.
© 2024 PatSnap. All rights reserved.Legal|Privacy policy|Modern Slavery Act Transparency Statement|Sitemap|About US| Contact US: help@patsnap.com