Catalyst component used for vinyl polymerization, preparation method and application
An ethylene polymerization and catalyst technology, applied in the field of olefin polymerization, can solve the problems of unsatisfactory hydrogen adjustment sensitivity, complicated operation and high production cost
- Summary
- Abstract
- Description
- Claims
- Application Information
AI Technical Summary
Problems solved by technology
Method used
Image
Examples
Embodiment 1
[0055] 1. Preparation of catalyst components
[0056] In a four-neck flask equipped with a stirrer, install a reflux condenser and connect a cumulative gas meter to the reflux condenser. After the entire reaction device is fully replaced by nitrogen, add 70.8ml of absolute ethanol and 1.26g of iodine to the container. , to dissolve it. Add 6g metal magnesium inside, be warming up to the reflux temperature of ethanol under stirring condition, add absolute ethanol 47ml every 10 minutes from reflux, magnesium powder 6g, altogether 3 times. About 1 to 2 hours after the completion of the third addition, the liquid viscosity began to rise sharply (at this time, the reaction rate can be calculated to be about 85% through the amount of hydrogen generated), at this time, add 259ml of ethanol to the reaction system, and continue the reaction until The whole reaction time is about 6 hours until no hydrogen gas is produced at the end of the reaction. The solid was washed three times wit...
Embodiment 2
[0064] Catalyst preparation method is the same as embodiment 1.
[0065] Polymerization evaluation conditions: a stainless steel reaction kettle with a volume of 2 liters, fully replaced by hydrogen gas, injecting about 0.5 liters of hexane with nitrogen, injecting 2 ml of triethylaluminum-hexane solution with a concentration of 1 mmol / ml with a syringe, and stirring Then add 10 mg of titanium-containing solid catalyst component, and make up about 1 liter of hexane in total.
[0066] After the feeding is completed, the temperature is raised and hydrogen and ethylene are introduced successively, of which 6.8×10 5 H 2 , 3.5×10 5 Pa ethylene, the polymerization temperature is 85°C, react for two hours, lower the temperature, drain the residual pressure in the kettle, release the polymer slurry material, filter off the hexane, dry the polymer to obtain polyethylene powder, the results are shown in Table 1.
Embodiment 3
[0068] The catalyst preparation method is the same as in Example 1, and the 2,2,2-trichloroethanol hexane solution (0.1M) is changed to 2ml.
[0069] After evaporating and drying, 6.5 g of granular titanium-containing solid catalyst components were obtained, including 1.98% Ti and 19.1% (by weight) of tetrahydrofuran.
[0070] Polymerization evaluation conditions are the same as in Example 1, and the results are shown in Table 1.
PUM
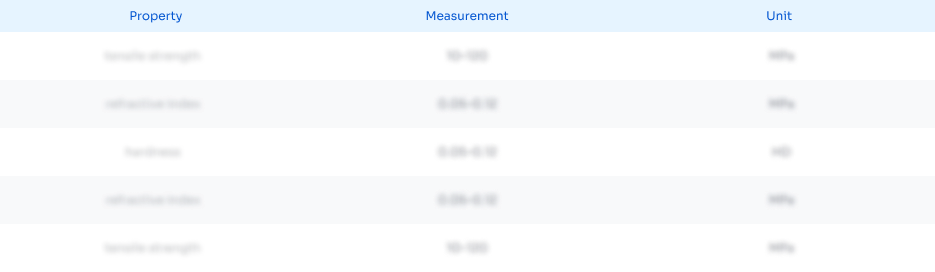
Abstract
Description
Claims
Application Information

- R&D
- Intellectual Property
- Life Sciences
- Materials
- Tech Scout
- Unparalleled Data Quality
- Higher Quality Content
- 60% Fewer Hallucinations
Browse by: Latest US Patents, China's latest patents, Technical Efficacy Thesaurus, Application Domain, Technology Topic, Popular Technical Reports.
© 2025 PatSnap. All rights reserved.Legal|Privacy policy|Modern Slavery Act Transparency Statement|Sitemap|About US| Contact US: help@patsnap.com