Improved synthesis method for glufosinate and analogue thereof
An analogue, glufosinate-ammonium technology, applied in the field of synthesis of glufosinate-ammonium and its analogues, can solve problems such as difficult to meet production requirements, harsh processing and manufacturing process requirements, and high risk, so as to reduce the cost of three wastes treatment and reduce production Cost, the effect of reducing the production of three wastes
- Summary
- Abstract
- Description
- Claims
- Application Information
AI Technical Summary
Problems solved by technology
Method used
Image
Examples
Embodiment 1
[0040] In a 500ml four-neck flask, add 23.5g of fresh magnesium chips (0.98mol), add THF100g, heat to 35°C and add 1g of methyl bromide dropwise for initiation. Chloromethane 49.5g (0.98mol). The process of passing through the chloromethane maintains a slight reflux state, and maintains a slight reflux state for 2 hours at the end of the passage, until there is almost no visible magnesium chips, and it is ready for use.
[0041] Add 110.7g (0.67mol) of triethyl phosphinate to another 1000ml four-neck flask, add 6g of caprolactam, add 45.8g (0.33mol) of phosphorus trichloride dropwise at 20-25°C, and keep warm for 2 hours after the dropping Diethyl chlorophosphonite is obtained.
[0042] After the above is completed, under strong stirring, add the Grignard reagent dropwise into the diethyl chlorophosphonite, the temperature of the addition is controlled at -10~-5°C, and the drop is completed within 3~4 hours. After the dropwise addition, 2.0 g of dry hydrogen chloride gas was...
Embodiment 2
[0044] Into a 500ml four-neck flask, add 23.2g of fresh magnesium chips (0.965mol), add THF100g, heat to 35°C and add 1g of methyl bromide dropwise for initiation. Chloromethane 48.7g (0.965mol). The process of passing through the chloromethane maintains a slight reflux state, and maintains a slight reflux state for 2 hours at the end of the passage, until there is almost no visible magnesium chips, and it is ready for use.
[0045] Add 110.7g (0.67mol) of triethyl phosphinate to another 1000ml four-neck flask, add 6g of hexamethylphosphonic acid triamide, add dropwise 45.8g (0.33mol) of phosphorus trichloride at 20-25°C, At the end of the dropwise addition, keep warm for 2 hours to obtain diethyl chlorophosphonite.
[0046] After the above is completed, add the Grignard reagent dropwise into the diethyl chlorophosphonite under strong stirring, and the dropping temperature is controlled at -10~-5°C, and the drop is completed in 4~6hr. After the dropwise addition, 5.0 g of dry ...
Embodiment 3
[0049] Add 11.42g of freshly distilled acrolein (0.204mol) dropwise to a mixture of 27.2g of diethyl methylphosphinate (0.2mol) and 46g of ethanol (1mol) under vigorous stirring at 20-30°C, dropwise The adding time is controlled for about 2 hours, and the dropping temperature is controlled at 15-20°C. After the dropwise addition, continue the heat preservation reaction at this temperature for 2 hours, and then recover the ethanol under negative pressure to 90°C / -0.09Mpa. 20g of 5% hydrochloric acid was added dropwise to the residue at 25-30°C, and the reaction was continued at this temperature for 2 hours, and then the ethanol produced by hydrolysis was removed under negative pressure to 60°C / -0.09Mpa. Add the residual material from the precipitation to 9.8g sodium cyanide (0.2mol) and 16.05g ammonium chloride (0.3mol) in 80ml 25% ammonia solution drop by drop, the dropping temperature is controlled at 20-25°C, and the dropping time is controlled for 2hr After the dropwise ad...
PUM
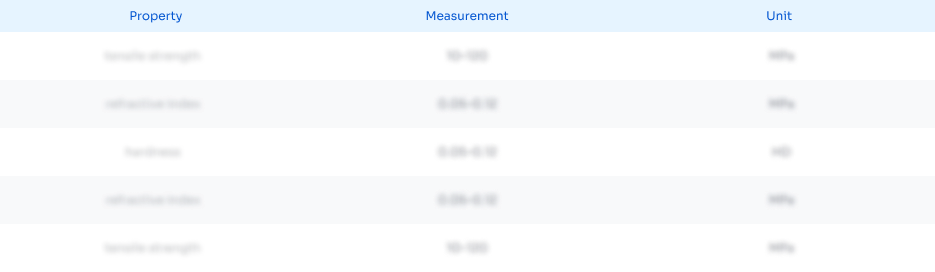
Abstract
Description
Claims
Application Information

- R&D
- Intellectual Property
- Life Sciences
- Materials
- Tech Scout
- Unparalleled Data Quality
- Higher Quality Content
- 60% Fewer Hallucinations
Browse by: Latest US Patents, China's latest patents, Technical Efficacy Thesaurus, Application Domain, Technology Topic, Popular Technical Reports.
© 2025 PatSnap. All rights reserved.Legal|Privacy policy|Modern Slavery Act Transparency Statement|Sitemap|About US| Contact US: help@patsnap.com