Al-Ni alloy electroplating method in low-temperature salt melting system
A low-temperature molten salt and system technology, applied in the field of electroplating, can solve problems such as difficult alloy plating, and achieve the effects of reducing the rate of defective products, improving ease of casting, and refining grains
- Summary
- Abstract
- Description
- Claims
- Application Information
AI Technical Summary
Problems solved by technology
Method used
Examples
Embodiment 1
[0017] with SmCl 3 +NiCl 2 +AlCl 3 +NaCl+KCl is the electrolyte system, AlCl 3 150g of NaCl, 19g of NaCl, and 25g of KCl; a 1mm thick low-carbon steel sheet is used as the cathode, 99% of the aluminum sheet is used as the anode, and the current density is 55mA·cm -2 , the electroplating temperature is controlled at 460K, the electroplating time is controlled at 20min, and the cell voltage is controlled at 2V. For the first plating, add 1.6gNiCl 2 , 0.18g SmCl 3 After dissolving for 10 minutes, insert the cathode and anode for electroplating, and the electroplating time is 20 minutes. Plating for the second time, add NiCl 2 0.3g, insert the cathode and anode for electroplating, and the electroplating time is 20min. Plating for the third time, add NiCl 2 0.3g, insert the cathode and anode for electroplating, and the electroplating time is 20min. SmCl can be added during 3 , but the total amount shall not exceed 0.4% of the total weight.
Embodiment 2
[0019] with CeCl 3 +MnCl 2 +AlCl 3 +NaCl+KCl is the electrolyte system, AlCl 3 150g of NaCl, 19g of NaCl, and 25g of KCl; a 1mm thick low-carbon steel sheet is used as the cathode, 99% of the aluminum sheet is used as the anode, and the current density is 55mA·cm -2 , the electroplating temperature is controlled at 460K, the electroplating time is controlled at 20min, and the cell voltage is controlled at 2V. For the first plating, add 1.5gNiCl 2 , 0.6g CeCl 3 After dissolving for 10 minutes, insert the cathode and anode for electroplating, and the electroplating time is 20 minutes. Plating for the second time, add NiCl 2 0.3g, insert the cathode and anode for electroplating, and the electroplating time is 20min. Plating for the third time, add NiCl 2 0.3g, insert the cathode and anode for electroplating, and the electroplating time is 20min. CeCl can be added during 3 , but the total amount shall not exceed 0.35% of the total weight.
PUM
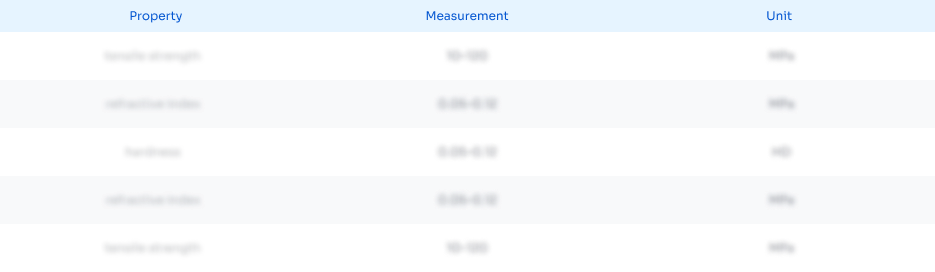
Abstract
Description
Claims
Application Information

- R&D Engineer
- R&D Manager
- IP Professional
- Industry Leading Data Capabilities
- Powerful AI technology
- Patent DNA Extraction
Browse by: Latest US Patents, China's latest patents, Technical Efficacy Thesaurus, Application Domain, Technology Topic, Popular Technical Reports.
© 2024 PatSnap. All rights reserved.Legal|Privacy policy|Modern Slavery Act Transparency Statement|Sitemap|About US| Contact US: help@patsnap.com