Device for recovering and utilizing waste heat generated by smoke discharging in split type heating medium circulating way
A waste heat recovery and recycling technology, used in heat exchange equipment, indirect heat exchangers, lighting and heating equipment, etc.
- Summary
- Abstract
- Description
- Claims
- Application Information
AI Technical Summary
Problems solved by technology
Method used
Image
Examples
Embodiment 1
[0017] It is used as a tubular flue gas-clean flue gas heat exchanger (tubular GGH) in the flue gas limestone-gypsum wet desulfurization system. At present, the most widely used desulfurization process in large coal-fired power plants is the limestone-gypsum wet desulfurization process. The flue gas temperature is generally around 45-50°C, so a flue gas-clean flue gas heat exchanger (GGH) is usually installed in this process. In the GGH, on the one hand, the untreated flue gas entering the absorption tower is transferred from ~130°C is lowered to about 90°C. On the other hand, the clean flue gas after washing, desulfurization and demisting is heated from about 50°C to 80°C and sent into the chimney to be discharged into the atmosphere.
[0018] The present invention can be used as a tubular GGH in a limestone-gypsum wet desulfurization system. Heat medium low temperature heat transfer oil. The heat-absorbing heat exchanger 1 of the present invention is used as a flue gas coo...
Embodiment 2
[0024] The heat release heat exchanger 2 of the present invention is used to preheat the combustion air entering the boiler to replace the air heater.
[0025] Place the heat-absorbing heat exchanger 1 of the present invention in the exhaust flue of the boiler to absorb the waste heat of exhaust smoke, place the heat-releasing heat exchanger 2 of the present invention at the heater of the boiler, and use the absorbed waste heat for preheating Combustion air entering the boiler, instead of the heater. Conventional air heaters need to use steam to heat the combustion air, which results in a significant increase in coal consumption of the unit. Since the circulating heat medium in the present invention is low-temperature heat-conducting oil, even in cold northern regions, when the ambient temperature is as low as -30°C to -50°C, safe work can still be guaranteed. In a word, in the cold region of the north, considering the two aspects of safety and economy, it is the best choice to...
Embodiment 3
[0027] The heat release heat exchanger of the present invention is used for preheating gas (natural gas or liquefied petroleum gas, etc.) of a gas furnace.
[0028] Heat-absorbing heat exchanger 1 of the present invention is placed in the exhaust flue of furnace kiln to absorb the waste heat of smoke exhaust, heat release heat exchanger 2 of the present invention is placed in the gas supply pipeline of furnace kiln, the waste heat absorbed It is used to preheat the gas (natural gas or liquefied petroleum gas, etc.) entering the kiln. The gas of the conventional gas-fired kiln is directly supplied, which causes a significant increase in the energy consumption of the unit. From an economic point of view, using the exhaust heat of the kiln to preheat the gas can achieve obvious economic benefits, see Figure 7 11 among the figure is a gas furnace, and 12 is an expansion tank.
PUM
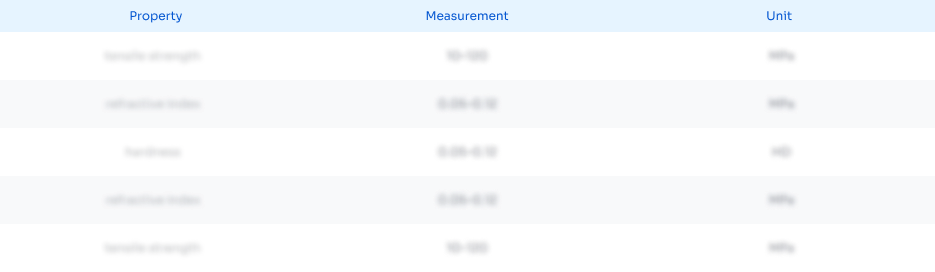
Abstract
Description
Claims
Application Information

- R&D Engineer
- R&D Manager
- IP Professional
- Industry Leading Data Capabilities
- Powerful AI technology
- Patent DNA Extraction
Browse by: Latest US Patents, China's latest patents, Technical Efficacy Thesaurus, Application Domain, Technology Topic, Popular Technical Reports.
© 2024 PatSnap. All rights reserved.Legal|Privacy policy|Modern Slavery Act Transparency Statement|Sitemap|About US| Contact US: help@patsnap.com