Method for separating ethylene glycol, propanediol and butanediol
A technology of propylene glycol and butanediol, which is applied in the separation/purification of hydroxyl compounds, organic chemistry, etc., can solve the problem of high energy consumption, and achieve the effect of low energy consumption for separation and energy saving
- Summary
- Abstract
- Description
- Claims
- Application Information
AI Technical Summary
Problems solved by technology
Method used
Image
Examples
Embodiment 1
[0014] according to figure 1 Shown flow process, water is with 2.00 g / min, methyl alcohol is with 4.00 g / min and raw material (ethylene glycol mass fraction is 85%, and 1,2-propanediol mass fraction is 10%, the quality of 1,2-butanediol Fraction is 5.00%) with 5.00 g / min respectively from the 1st, 3rd and 6th beds of the simulated moving bed with bed number of 10, and Su Qing brand DA201-C resin is filled in the bed, operating pressure is normal pressure, operating The temperature is 40°C and the space velocity is 1.5hr -1 , the flow rate of the mixture of resolving agent and 1,2-butanediol from bed 2 is 1.50 g / min, the flow rate of the mixture of resolving agent and 1,2-propylene glycol from bed 4 is 3.25 g / min, Layer 9 obtains the mixture flow rate of resolving agent and ethylene glycol to be 5.25 g / min, and the three streams of extraction pass through 1,2-butanediol separation tower, 1,2-propanediol separation tower and ethylene glycol separation tower respectively, and pa...
Embodiment 2
[0016] by similar figure 1 Shown flow process, methyl alcohol is with 0.50 g / min, ethanol with 0.50 g / min and raw material (ethylene glycol mass fraction is 95%, 1,3-propanediol mass fraction is 3%, 1,4-butanediol mass fraction 2%) with 5.00 g / min respectively from the 1st, 3rd and 5th bed layers of the simulated moving bed with 6 bed layers, the Su Qing brand DA201-A resin is filled in the bed layer, the operating pressure is 1MPa, and the operating temperature is 20℃, space velocity is 0.2hr -1 , the flow rate of the mixture of resolving agent and 1,4-butanediol from bed 2 is 0.40 g / min, the flow rate of the mixture of resolving agent and 1,3-propylene glycol from the 4th bed layer is 0.45 g / min, from the bed Layer 6 obtains the mixture flow rate of resolving agent and ethylene glycol to be 5.15 g / min, and the three streams of extraction pass through 1,4-butanediol separation tower, 1,3-propanediol separation tower and ethylene glycol separation tower respectively, and pass...
Embodiment 3
[0018] by similar figure 1Shown flow process, methyl alcohol is with 10.00 g / min, acetone is with 10.00 g / min and raw material (ethylene glycol mass fraction is 60%, 1,2-propanediol mass fraction is 15%, 1,3-butanediol mass fraction 25%) at 5.00 g / min respectively from the 1st, 8th and 20th beds of the simulated moving bed with 30 bed layers, filled with Su Qing brand DA201-D resin in the bed layer, the operating pressure is 0.5MPa, and the operating temperature 50℃, space velocity 5.0hr -1 , from the bed layer 6, the flow rate of the mixture of resolving agent and 1,3-butanediol is 9.65 g / min, and the flow rate of the mixture of resolving agent and 1,2-propylene glycol from the 15th bed layer is 8.75 g / min. Layer 26 obtains the flow rate of the mixture of resolving agent and ethylene glycol to be 6.60 g / min, and the three streams produced are respectively through 1,3-butanediol separation tower, 1,2-propanediol separation tower and ethylene glycol separation tower. Ordinary...
PUM
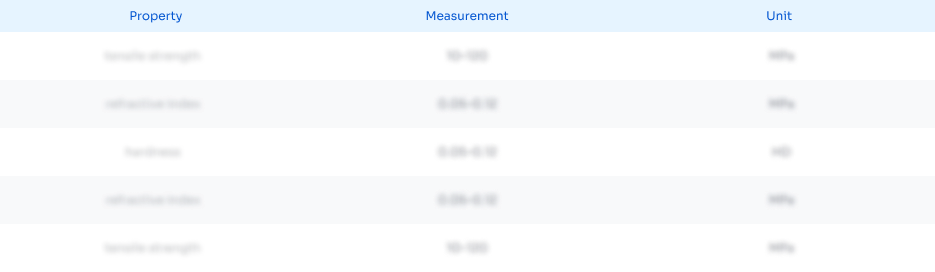
Abstract
Description
Claims
Application Information

- R&D
- Intellectual Property
- Life Sciences
- Materials
- Tech Scout
- Unparalleled Data Quality
- Higher Quality Content
- 60% Fewer Hallucinations
Browse by: Latest US Patents, China's latest patents, Technical Efficacy Thesaurus, Application Domain, Technology Topic, Popular Technical Reports.
© 2025 PatSnap. All rights reserved.Legal|Privacy policy|Modern Slavery Act Transparency Statement|Sitemap|About US| Contact US: help@patsnap.com