Lightweight foam concrete insulating brick and its manufacturing method
A technology of foam concrete and thermal insulation bricks, which is applied in the field of building wall masonry materials, can solve the problems of flammable thermal insulation materials, high construction cost, and non-thermal insulation of wall materials, so as to reduce the use, save energy and protect the cost of environmental protection , The effect of reducing construction costs
- Summary
- Abstract
- Description
- Claims
- Application Information
AI Technical Summary
Problems solved by technology
Method used
Examples
Embodiment Construction
[0013] It can use industrial waste, tailings slag, packaging waste polystyrene foam, 42.5R ordinary silicon cement, quicklime powder, quick gypsum powder, admixture materials, activator, early strength agent, slag, waste expanded perlite and other raw materials to mix design.
[0014] The components include aggregates, cementitious materials, admixtures, and functional auxiliary materials. The admixture can improve and improve the performance of the cementitious material, and the functional auxiliary material can improve and enhance the light weight, heat preservation and durability of the aggregate. These four components are a unified whole, and the resulting effects are synergistically superimposed, fully endowing the lightweight insulation brick with ideal design performance. The better the cooperation between them, the better the performance of lightweight insulation bricks.
[0015] Aggregate is the main support for constituting the main frame of the material and bearin...
PUM
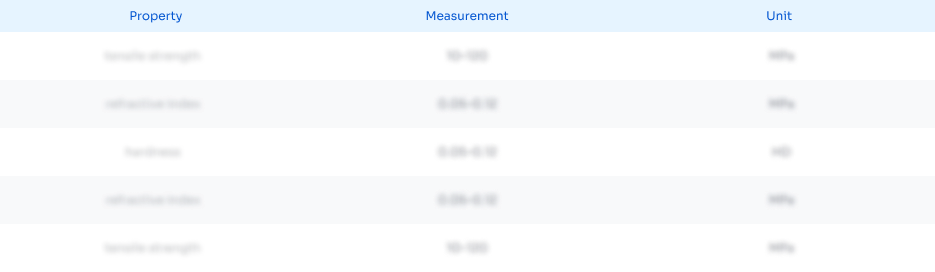
Abstract
Description
Claims
Application Information

- R&D
- Intellectual Property
- Life Sciences
- Materials
- Tech Scout
- Unparalleled Data Quality
- Higher Quality Content
- 60% Fewer Hallucinations
Browse by: Latest US Patents, China's latest patents, Technical Efficacy Thesaurus, Application Domain, Technology Topic, Popular Technical Reports.
© 2025 PatSnap. All rights reserved.Legal|Privacy policy|Modern Slavery Act Transparency Statement|Sitemap|About US| Contact US: help@patsnap.com