Waste heat recovery device of calcinator
A waste heat recovery device and waste heat recovery technology, applied in furnaces, waste heat treatment, furnace components, etc., can solve problems such as energy loss, and achieve the effect of easy and simple implementation
- Summary
- Abstract
- Description
- Claims
- Application Information
AI Technical Summary
Problems solved by technology
Method used
Image
Examples
Embodiment Construction
[0021] The present invention will be described in further detail below in conjunction with the accompanying drawings and specific embodiments.
[0022] Such as figure 1 As shown, the roaster waste heat recovery device of the present invention is provided with at least one waste heat recovery heat exchanger 5, and this embodiment is one. A smoke exhauster 3 is provided between the waste heat recovery heat exchanger 5 and the roasting furnace 1, and the smoke exhauster 3 and the roasting furnace 1 are connected through the front smoke pipe 2 of the smoke exhauster, and the smoke exhauster 3 and the waste heat recovery heat exchanger 5 are connected through the rear smoke pipe 4 of the exhaust machine, the waste heat recovery heat exchanger 5 and the chimney 7 are connected through the chimney front smoke pipe 6, the upper part of the waste heat recovery heat exchanger 5 is connected with the cold water pipe 8, and the waste heat recovery heat exchange The bottom of device 5 com...
PUM
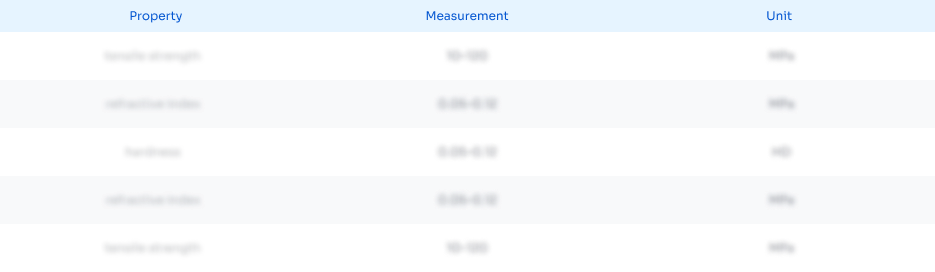
Abstract
Description
Claims
Application Information

- Generate Ideas
- Intellectual Property
- Life Sciences
- Materials
- Tech Scout
- Unparalleled Data Quality
- Higher Quality Content
- 60% Fewer Hallucinations
Browse by: Latest US Patents, China's latest patents, Technical Efficacy Thesaurus, Application Domain, Technology Topic, Popular Technical Reports.
© 2025 PatSnap. All rights reserved.Legal|Privacy policy|Modern Slavery Act Transparency Statement|Sitemap|About US| Contact US: help@patsnap.com