Ammonia recovery process and equipment for non-ferrous metal metallurgical industry
A technology for the recovery of non-ferrous metals and ammonia, applied in the field of ammonia recovery, can solve the problems of low efficiency of bubble-cap trays, affecting normal production, affecting normal operation, etc., to improve production efficiency and economic benefits, good economic and environmental benefits, Good effect of self-cleaning ability
- Summary
- Abstract
- Description
- Claims
- Application Information
AI Technical Summary
Problems solved by technology
Method used
Image
Examples
Embodiment 1
[0022] Alkali 0.25 ton / ton of raw material liquid that mixes alkali tank 3, alkali lye is the NaOH aqueous solution of mass concentration 40%, after lye pump 6 pressurization, with raw material liquid 4 tons / hour (the total of 25% of mass concentration Ammonia content) after raw material pump 7 pressurization, after the two are mixed in pipeline, be sent to the top of ammonia distillation tower 1 (operating pressure 0.3MPa gauge pressure, tray layer number 15 layers), the ammonia in raw material liquid is by The steam provided by the reboiler 5 is stripped and removed, and the solution with an ammonia content of 150 ppm is obtained at the bottom of the ammonia distillation tower 1, and is sent to the next process; the vapor phase ammonia at the top of the ammonia distillation tower 1 passes through the ammonia splitter 4 After condensation, high-concentration ammonia vapor (mass concentration 70%) is obtained and enters the bottom of ammonia recovery tower 2 (operating pressure...
Embodiment 2
[0024]The NaOH aqueous solution 0.5 ton / ton raw material liquid of the mass concentration 20% that comes from alkali tank 3, after lye pump 6 pressurization, with raw material liquid 4 tons / hour (the total ammonia content of mass concentration 25%) through raw material pump 7. After pressurization, after the two are mixed in the pipeline, they are sent to the top of the ammonia distillation tower 1 (working pressure 0.5MPa gauge pressure, 20 tray layers), and the ammonia in the raw material liquid is provided by the reboiler 5. The steam is stripped and removed, and the bottom of the ammonia distillation tower 1 obtains a solution with an ammonia content of 120 ppm, which is sent to the next process; the vapor-phase ammonia at the top of the ammonia distillation tower 1 is condensed by the ammonia splitter 4 to obtain a high concentration. Ammonia vapor (mass concentration 70%) enters the bottom of ammonia recovery tower 2 (operating pressure 0.35MPa gauge pressure, 15 layers o...
Embodiment 3
[0026] 1 ton / ton of NaOH aqueous solution 1 ton / ton raw material liquid of the mass concentration 10% that comes from alkali tank 3, after lye pump 6 pressurization, with raw material liquid 4 tons / hour (the total ammonia content of mass concentration 25%) through raw material pump 7 After pressurization, after the two are mixed in the pipeline, they are sent to the top of the ammonia distillation tower 1 (working pressure 0.7MPa gauge pressure, 35 layers of trays), and the ammonia in the raw material liquid is provided by the reboiler 5. The steam is stripped and removed, and the bottom of the ammonia distillation tower 1 obtains a solution with an ammonia content of 100 ppm, which is sent to the next process; the vapor-phase ammonia at the top of the ammonia distillation tower 1 is condensed by the ammonia splitter 4 to obtain a high concentration. Ammonia vapor (mass concentration 70%) enters the bottom of ammonia recovery tower 2 (operating pressure 0.55MPa gauge pressure, ...
PUM
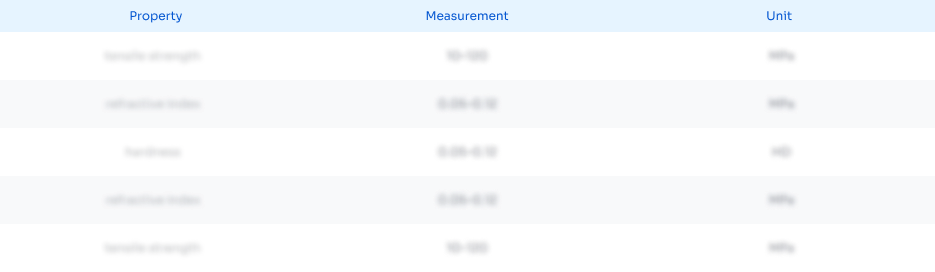
Abstract
Description
Claims
Application Information

- Generate Ideas
- Intellectual Property
- Life Sciences
- Materials
- Tech Scout
- Unparalleled Data Quality
- Higher Quality Content
- 60% Fewer Hallucinations
Browse by: Latest US Patents, China's latest patents, Technical Efficacy Thesaurus, Application Domain, Technology Topic, Popular Technical Reports.
© 2025 PatSnap. All rights reserved.Legal|Privacy policy|Modern Slavery Act Transparency Statement|Sitemap|About US| Contact US: help@patsnap.com