Continuous casting production process for improving quality of free cutting steel casting blank
A production process and steel casting technology, applied in the field of free-cutting steel production process, can solve problems such as difficult separation, surface pinholes, skin turning, etc., to prevent segregation of lead components, improve internal cracks, and improve the quality of casting billets.
- Summary
- Abstract
- Description
- Claims
- Application Information
AI Technical Summary
Problems solved by technology
Method used
Image
Examples
Embodiment 1
[0032] Example 1. When producing lead-free free-cutting steel. Taking Y45 free-cutting steel as an example, its main chemical composition is shown in the following table:
[0033] C%
Si%
Mn%
P%
S%
0.48
0.25
0.70
0.020
0.028
[0034] The balance is Fe and unavoidable impurities. When continuously casting a billet with a cross-sectional size of 150mm×150mm, the casting superheat is controlled at 15-45°C, the casting speed is controlled at 1.70-2.45m / min, and it is best to control the casting superheat at 15-25°C , The billet casting speed is controlled at 2.00-2.20m / min, and the casting speed increases with the decrease of superheat. The amplitude of the crystallizer is controlled at 3-8mm, the vibration frequency of the mold is controlled at 150-300cpm, the negative slip rate is controlled at -20--80%, the distance between the vibration marks of the slab is controlled at 6-11mm, the secondary cooling wate...
Embodiment 2
[0038] Example 2. When producing leaded free-cutting steel. Taking Y45Pb as an example, its main chemical composition is shown in the following table:
[0039] C%
Si%
Mn%
P%
S%
Pb%
0.48
0.25
0.70
0.020
0.028
0.21
[0040] The balance is Fe and unavoidable impurities. When continuously casting a billet with a cross-sectional size of 150mm×150mm, the casting superheat is controlled at 15-45°C, and the billet casting speed is controlled at 1.70-2.45; it is best to control the casting superheat at 15-25°C. The blank casting speed is controlled at 2.00-2.20m / min, and the casting speed increases with the decrease of superheat. The amplitude of the crystallizer is controlled at 3-8mm, the vibration frequency of the mold is controlled at 150-300cpm, the negative slip rate is controlled at -20--80%, the distance between the vibration marks of the slab is controlled at 6-11mm, the secondary cooling water...
PUM
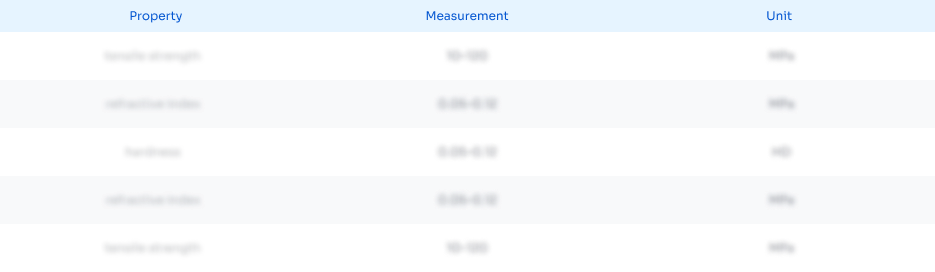
Abstract
Description
Claims
Application Information

- R&D
- Intellectual Property
- Life Sciences
- Materials
- Tech Scout
- Unparalleled Data Quality
- Higher Quality Content
- 60% Fewer Hallucinations
Browse by: Latest US Patents, China's latest patents, Technical Efficacy Thesaurus, Application Domain, Technology Topic, Popular Technical Reports.
© 2025 PatSnap. All rights reserved.Legal|Privacy policy|Modern Slavery Act Transparency Statement|Sitemap|About US| Contact US: help@patsnap.com