Velocity Planning Method of Double Nurbs Tool Trajectory in Five-axis NC Machining
A tool path and speed planning technology, applied in the field of CNC machine tools, can solve problems such as affecting the efficiency of processing, lack of real-time, affecting the quality of the processed surface, etc., to achieve the effect of improving processing efficiency, ensuring processing accuracy, and high computing efficiency
- Summary
- Abstract
- Description
- Claims
- Application Information
AI Technical Summary
Problems solved by technology
Method used
Image
Examples
Embodiment 1
[0039] This embodiment is based on the dynamic constraints of the five-axis machine tool for the speed planning method of the dual NURBS curve tool trajectory, which is divided into two steps:
[0040] 1. Establishment of comprehensive constraints for dual NURBS curve interpolation based on the dynamic characteristics of a five-axis machine tool.
[0041] 1) Establish the tool speed distribution field model in the dual NURBS curve tool trajectory and solve the maximum feasible feed rate constraint determined by it.
[0042] Such as figure 1 As shown, the double NURBS curve is an equidistant double NURBS tool path, P(u) represents the tool center point NURBS curve, Q(u) represents the tool axis point NURBS curve, and the point on the curve P(u) represents the tool position point, through The point connecting P(u) and Q(u) at the corresponding parameter indicates the direction of the tool axis, which is denoted as D(u), that is, D(u)=P(u)-Q(u).
[0043] in:
[0044] The tool ce...
Embodiment 2
[0075] First establish the tool velocity field distribution, record the NURBS curve of the tool center point as P(u), the tool axis point NURBS curve as Q(u), and the tool direction as D(u), then D(u)=P(u)- Q(u). Note that |D(u)|=H, then the unit vector of the tool direction can be expressed as Then the point on the tool axis can be expressed as B(u, l)=P(u)+lO(u), where l is the distance from the point on the tool axis to the center point of the tool. By deriving time on both sides of the equation, the velocity at any point on the tool axis can be found. By limiting the feed speed of the tool along the machining path, the speed of any point on the tool axis can be achieved first, and the resulting constraint is called the constraint of the tool speed field on the maximum feed speed.
[0076] Next, establish the constraints of the tool scanning area on the feed rate. Firstly, establish the formula for the scanning area of the tool axis:
[0077] S ...
PUM
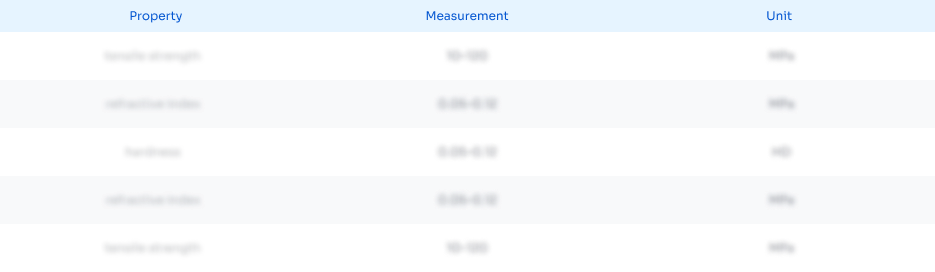
Abstract
Description
Claims
Application Information

- R&D
- Intellectual Property
- Life Sciences
- Materials
- Tech Scout
- Unparalleled Data Quality
- Higher Quality Content
- 60% Fewer Hallucinations
Browse by: Latest US Patents, China's latest patents, Technical Efficacy Thesaurus, Application Domain, Technology Topic, Popular Technical Reports.
© 2025 PatSnap. All rights reserved.Legal|Privacy policy|Modern Slavery Act Transparency Statement|Sitemap|About US| Contact US: help@patsnap.com