Manufacturing method and structure of embossed release paper
A manufacturing method and technology of release paper, applied in paper, papermaking, specialty paper, etc., can solve the problems of increased cost, production time and personnel waste, etc.
- Summary
- Abstract
- Description
- Claims
- Application Information
AI Technical Summary
Problems solved by technology
Method used
Image
Examples
Embodiment Construction
[0026] In order to further have a clear and detailed understanding and understanding of the structure, use and characteristics of the present invention, the preferred embodiments are now cited, and detailed descriptions are as follows in conjunction with the accompanying drawings:
[0027] First, see Figure 1 to Figure 2 As shown, the embossed release paper manufacturing method of the present invention includes the following steps: firstly, the servo motor of an unwind machine 10 (unwind machine) is started to drive the reel, and the entire roll of sheet substrate 20 is continuously rolled out to A dipping roller 11 (dipping roller) is used for gluing.
[0028] The above-mentioned dipping roller 11 (dipping roller) is combined with a pressure roller 12 to evenly coat a release agent on the surface of the sheet-shaped substrate 20, and the above-mentioned sheet-shaped substrate 20 is located between the dipping roller 11 and the pressure roller 12 Glue is conveyed between the...
PUM
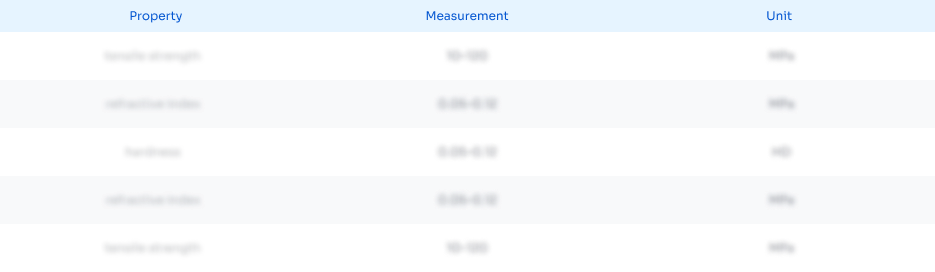
Abstract
Description
Claims
Application Information

- R&D
- Intellectual Property
- Life Sciences
- Materials
- Tech Scout
- Unparalleled Data Quality
- Higher Quality Content
- 60% Fewer Hallucinations
Browse by: Latest US Patents, China's latest patents, Technical Efficacy Thesaurus, Application Domain, Technology Topic, Popular Technical Reports.
© 2025 PatSnap. All rights reserved.Legal|Privacy policy|Modern Slavery Act Transparency Statement|Sitemap|About US| Contact US: help@patsnap.com