A kind of semi-hard magnetic material and preparation method thereof
A semi-hard magnetic, mass percentage technology, applied in the direction of magnetic materials, magnetic objects, electrical components, etc., can solve the problems of low utilization rate and high cost of cold rolling process materials, and achieve the effect of avoiding magnetic flux leakage
- Summary
- Abstract
- Description
- Claims
- Application Information
AI Technical Summary
Problems solved by technology
Method used
Examples
Embodiment 1
[0015] 1) Put iron, nickel, boron, and silicon into the steelmaking furnace. The mass percentages of iron, nickel, boron, and silicon are 55%, 32%, 8%, and 5%. The steelmaking temperature is 2700°C, and the melting temperature is 1.5 hours, the tapping temperature is 2000°C.
[0016] 2) The molten alloy obtained in step 1) is sprayed, the speed of the spray roller is 700 rpm, and the molten alloy is sprayed on the circumferential surface of the spray roller rotating at a high speed, protected by argon until the alloy on the surface of the roller is solidified to form an alloy sheet Finally, the alloy sheet is removed from the surface of the roller.
Embodiment 2
[0018] 1) Put iron, nickel, boron, and silicon into a steelmaking furnace. The mass percentages of iron, nickel, boron, and silicon are 65%, 22%, 7%, and 6%, and the steelmaking temperature is 2800°C. hours, the tapping temperature is 2100°C.
[0019] 2) Spray the molten alloy obtained in step 1), spray the molten alloy at a speed of 800 rpm on the spray roller, and spray the molten alloy on the circumferential surface of the spray roller rotating at a high speed, under argon protection, until the alloy on the surface of the roller is solidified to form an alloy sheet Finally, the alloy sheet is removed from the surface of the roller.
Embodiment 3
[0021] 1) Put iron, nickel, boron, and silicon into the steelmaking furnace. The mass percentages of iron, nickel, boron, and silicon are 62%, 28%, 5%, and 5%. The steelmaking temperature is 2900°C, and the melting temperature is 2.5 hours, the tapping temperature is 2500°C.
[0022] 2) The molten alloy obtained in step 1) is sprayed, the speed of the spray roll is 900 rpm, and the molten alloy is sprayed on the circumferential surface of the spray roll rotating at a high speed, protected by argon until the alloy on the surface of the roll is solidified to form an alloy sheet Finally, the alloy sheet is removed from the surface of the roller.
PUM
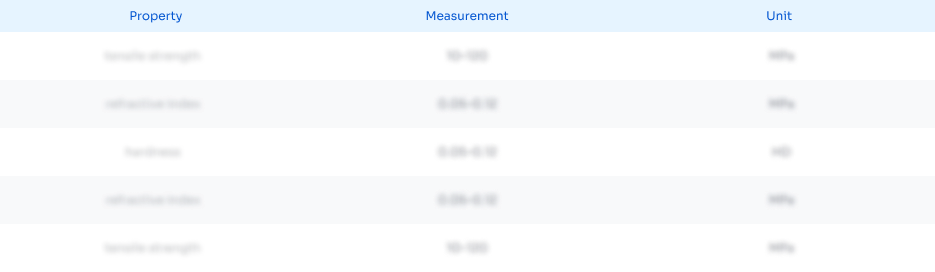
Abstract
Description
Claims
Application Information

- R&D
- Intellectual Property
- Life Sciences
- Materials
- Tech Scout
- Unparalleled Data Quality
- Higher Quality Content
- 60% Fewer Hallucinations
Browse by: Latest US Patents, China's latest patents, Technical Efficacy Thesaurus, Application Domain, Technology Topic, Popular Technical Reports.
© 2025 PatSnap. All rights reserved.Legal|Privacy policy|Modern Slavery Act Transparency Statement|Sitemap|About US| Contact US: help@patsnap.com