Electric heating friction spot welding stirring head and its welding method
A stirring head and friction point technology, applied in the field of electric heating friction spot welding stirring head and its welding, can solve the problems of insufficient flow, difficult to form welds, limited friction heat, etc. The effect of improved shear tensile properties and increased width of the connection zone
- Summary
- Abstract
- Description
- Claims
- Application Information
AI Technical Summary
Problems solved by technology
Method used
Image
Examples
example 1
[0011] Before welding, the surface of the 2.5mm magnesium alloy AZ31 flat plate is ground and fixed on the clamping device, and the temperature of the high-temperature electric heating coil is adjusted to raise the temperature of the stirring head to 480°C, and then welding is performed after stabilization. During the friction stir spot welding process, the heating temperature of the high-temperature electric heating coil remains constant until the end of the welding process.
example 2
[0013] Before welding, the surface of the 2.5mm magnesium alloy AZ31 flat plate is ground and fixed on the clamping device, and the temperature of the high-temperature electric heating coil is adjusted to raise the temperature of the stirring head to 490°C, and welding is performed after stabilization. During the friction stir spot welding process, the heating temperature of the high-temperature electric heating coil remains constant until the end of the welding process.
example 3
[0015] Before welding, the surface of the 2.5mm magnesium alloy AZ31 plate is ground and fixed on the clamping device, and the temperature of the high-temperature electric heating coil is adjusted to raise the temperature of the stirring head to 500°C, and welding is performed after stabilization. During the friction stir spot welding process, the heating temperature of the high-temperature electric heating coil remains constant until the end of the welding process.
PUM
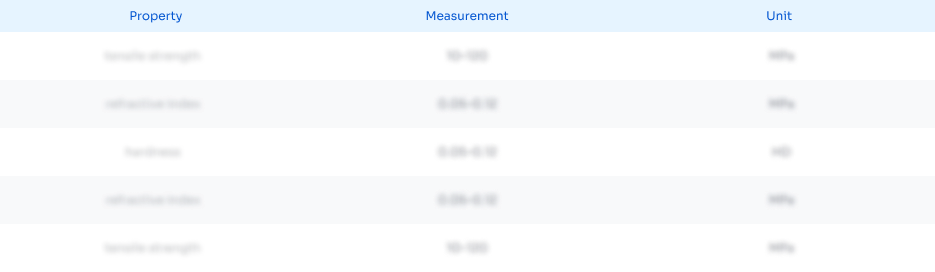
Abstract
Description
Claims
Application Information

- R&D
- Intellectual Property
- Life Sciences
- Materials
- Tech Scout
- Unparalleled Data Quality
- Higher Quality Content
- 60% Fewer Hallucinations
Browse by: Latest US Patents, China's latest patents, Technical Efficacy Thesaurus, Application Domain, Technology Topic, Popular Technical Reports.
© 2025 PatSnap. All rights reserved.Legal|Privacy policy|Modern Slavery Act Transparency Statement|Sitemap|About US| Contact US: help@patsnap.com