Etching method of single crystal silicon material for solar cell
A solar cell and crystalline silicon technology, applied in the field of solar cell material processing, can solve the problems of high manufacturing cost, complex auxiliary equipment, serious environmental pollution, etc., and achieve the effect of improving efficiency and photoelectric conversion efficiency
- Summary
- Abstract
- Description
- Claims
- Application Information
AI Technical Summary
Problems solved by technology
Method used
Examples
Embodiment 1
[0019] The polysilicon material is placed in the carrier boat in the vacuum reaction chamber. After the reaction chamber is closed, the cleaning gas nitrogen is introduced first, and then the mixed reaction gas of chlorine, sulfur hexafluoride and oxygen is passed into the reaction chamber, and the gas pressure is controlled to be 200Pa, the total gas flow rate is 1000ml / min, the flow ratio of chlorine: sulfur hexafluoride: oxygen is 1:2:2, and a high-frequency electricity with a frequency of 450KHz is applied to the reaction chamber; Nitrogen gas is introduced into the reaction chamber to clean up the remaining reaction mixture gas.
[0020] The polysilicon material processed by the above-mentioned texturing method has a four-sided pyramid structure, and the above-mentioned polysilicon material with a four-sided pyramid structure is used to make solar cells, and the photoelectric conversion efficiency can reach 18%. The photoelectric conversion efficiency of the fabricated so...
Embodiment 2
[0022] The single crystal silicon material is placed in the carrier boat in the vacuum reaction chamber. After the reaction chamber is closed, the cleaning gas helium is introduced first, and then the mixed gas of bromine, sodium hydroxide and oxygen is introduced into the reaction chamber to control the gas flow. The pressure is 180Pa, the total gas flow rate is 2500ml / min, the flow ratio of each gas is: 15:2:28, and high-frequency electricity with a frequency of 14MH is applied to the reaction chamber; after the reaction is completed, it is passed into the reaction chamber Helium, to clean the rest of the reaction gas mixture.
[0023] The monocrystalline silicon material processed by the above-mentioned texturing method has a square pyramid structure with uniform size, and the above-mentioned monocrystalline silicon material with the square pyramid structure is used to make solar cells, and the photoelectric conversion efficiency can reach 19%; under the same conditions The...
Embodiment 3
[0025] The polycrystalline silicon material and single crystal silicon material are placed together in the carrier boat in the vacuum reaction chamber. After the reaction chamber is closed, the cleaning gas nitrogen is first introduced into the reaction chamber, and then nitric acid gas, chlorine gas, sulfur hexafluoride and Oxygen mixed reaction gas, the control gas pressure is 230Pa, the total gas flow rate is 1800ml / min, and high-frequency electricity with a frequency of 12.5MHz is applied to the reaction chamber; after the reaction is completed, air is introduced into the reaction chamber, and the remaining The reaction mixture gas is cleaned.
[0026] The above-mentioned polycrystalline silicon material and monocrystalline silicon with four-sided pyramid structure are used to make solar cells respectively, and their photoelectric conversion efficiencies can reach 18% and 19% respectively; , and the photoelectric conversion efficiencies are 16.6% and 18% respectively; the ...
PUM
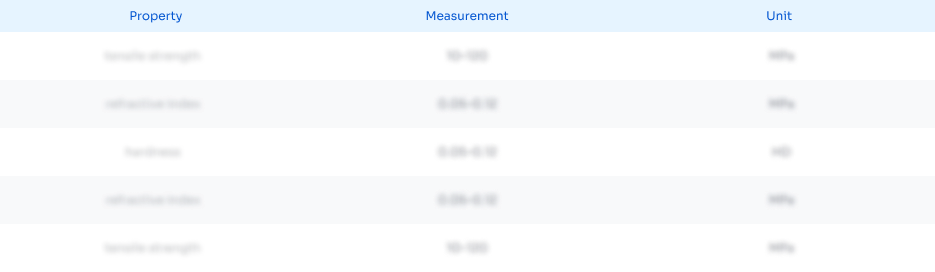
Abstract
Description
Claims
Application Information

- Generate Ideas
- Intellectual Property
- Life Sciences
- Materials
- Tech Scout
- Unparalleled Data Quality
- Higher Quality Content
- 60% Fewer Hallucinations
Browse by: Latest US Patents, China's latest patents, Technical Efficacy Thesaurus, Application Domain, Technology Topic, Popular Technical Reports.
© 2025 PatSnap. All rights reserved.Legal|Privacy policy|Modern Slavery Act Transparency Statement|Sitemap|About US| Contact US: help@patsnap.com