Manufacturing process for bolt with high strength of more than phi 30
A high-strength bolt and manufacturing process technology, used in the manufacture of tools, bolts, threaded fasteners, etc., can solve the problems of long heating time, high temperature, and easy formation of oxide layers on bolts, so as to refine grains and avoid crystallites. coarse grain effect
- Summary
- Abstract
- Description
- Claims
- Application Information
AI Technical Summary
Problems solved by technology
Method used
Examples
Embodiment 1
[0019] 42CrMo steel is selected as the raw material. According to the wire diameter requirements of the bolt, the raw material is pretreated and then heated forging. The heating forging temperature is 1100 ° C, and the heating forging time is 5 minutes. After heating forging, the corners of the high-strength bolt head of the present invention The hardness is HRC45, and the metallographic structure is martensite. The workpiece after heating and forging is quickly sent to the mesh belt furnace for high temperature tempering. After the workpiece enters the mesh belt furnace, it first passes through the preheating zone of the mesh belt furnace. Preheat at the temperature for 30 minutes, then enter the first heating zone and the second heating zone, heat at 570°C for 30 minutes after entering the first heating zone, then enter the second heating zone, heat at 570°C 30 minutes, and finally enter the heat preservation zone for heat preservation, at 570 ° C for 60 minutes.
[0020] Ta...
Embodiment 2
[0022] 42CrMo steel is selected as the raw material. According to the requirements of the wire diameter of the bolt, the raw material is pretreated and then heated forging. The heating forging temperature is 1200°C, and the heating forging time is 3 minutes. The hardness is HRC50, and the metallographic structure is martensite. The workpiece after heating and forging is quickly sent to the mesh belt furnace for high temperature tempering. After the workpiece enters the mesh belt furnace, it first passes through the preheating zone of the mesh belt furnace. Preheat at the temperature for 30 minutes, then enter the first heating zone and the second heating zone, heat at 560°C for 35 minutes after entering the first heating zone, then enter the second heating zone, heat at 560°C 30 minutes, and finally enter the heat preservation zone for heat preservation, at 560°C for 70 minutes.
[0023] Take out the workpiece after high temperature tempering and cool it with water. The metall...
Embodiment 3
[0025] 42CrMo steel is selected as the raw material. According to the requirements of the wire diameter of the bolt, the raw material is pretreated and then heated forging. The heating forging temperature is 1300°C, and the heating forging time is 2 minutes. The hardness is HRC55, and the metallographic structure is martensite. The workpiece after heating and forging is quickly sent to the mesh belt furnace for high temperature tempering. Preheat at the temperature for 40 minutes, enter the first heating zone and heat at 550°C for 40 minutes, then enter the second heating zone, heat at 550°C for 40 minutes, and finally enter the holding zone for heat preservation, at 550°C C for 80 minutes.
[0026] Take out the workpiece after high-temperature tempering, and cool it with water. The metallographic structure of the workpiece after tempering is pearlite and ferrite. The hardness of the workpiece is tested. The surface hardness of the workpiece after tempering is HRC35. The work...
PUM
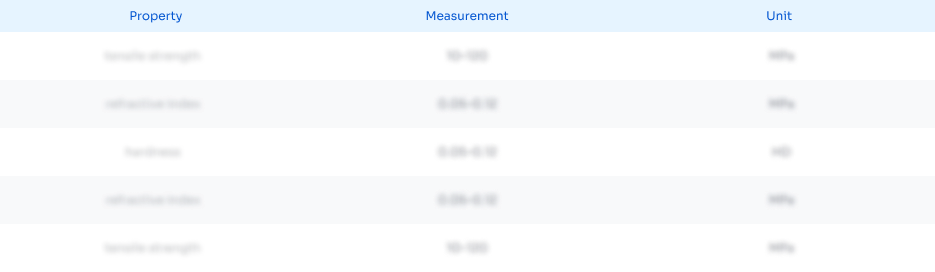
Abstract
Description
Claims
Application Information

- R&D
- Intellectual Property
- Life Sciences
- Materials
- Tech Scout
- Unparalleled Data Quality
- Higher Quality Content
- 60% Fewer Hallucinations
Browse by: Latest US Patents, China's latest patents, Technical Efficacy Thesaurus, Application Domain, Technology Topic, Popular Technical Reports.
© 2025 PatSnap. All rights reserved.Legal|Privacy policy|Modern Slavery Act Transparency Statement|Sitemap|About US| Contact US: help@patsnap.com