Paper pulp high density bleaching method
A technology of pulp and bleaching chambers, applied in pulp bleaching, pulp dehydration, etc., can solve the problems of high-concentration pulp bleaching that is difficult to apply in engineering, difficult to exceed 25%, and low transmission efficiency, so as to reduce the consumption of bleaching chemicals and electricity consumption. Consumption, reduce the effect of heat energy
- Summary
- Abstract
- Description
- Claims
- Application Information
AI Technical Summary
Problems solved by technology
Method used
Image
Examples
Embodiment 1
[0027] (1) Concentrate the unbleached masson pine chemical pulp with a concentration of 17% after washing to obtain a concentrated pulp with a concentration of 26.2%;
[0028] (2) Extruding and dehydrating the concentrated pulp with a parallel twin-screw extruder at a compression ratio of >3.0 to obtain a high-consistency pulp with a concentration of more than 30%;
[0029] (3) Pump hydrogen peroxide and bleaching auxiliaries into the high-concentration slurry at a pressure of 0.5 MPa at the extrusion exit of the parallel twin-screw press to obtain a mixture of ingredients and chemicals; bleaching auxiliaries include hydrogen Sodium oxide, chelating agent, stabilizer; relative to the dry pulp quality, the amount of hydrogen peroxide is 3.5%, the amount of sodium hydroxide is 2.5%, the amount of DTPA is 0.3%, and the amount of sodium silicate is 0.5%;
[0030] (4) Convey the material and drug mixture to the high-concentration bleaching chamber with a feeding screw, add saturate...
Embodiment 2
[0034] (1) Concentrate the unbleached eucalyptus chemical pulp with a concentration of 20% after washing to obtain a concentrated pulp with a concentration of 28%;
[0035] (2) Extruding and dehydrating the concentrated pulp with a parallel twin-screw extruder at a compression ratio of >3.0 to obtain a high-consistency pulp with a concentration of more than 30%;
[0036] (3) Pump hydrogen peroxide and bleaching auxiliaries into the high-concentration slurry at a pressure of 1.0 MPa at the extrusion exit of the parallel twin-screw press to obtain a mixture of ingredients and chemicals; the bleaching auxiliaries include hydrogen Sodium oxide, chelating agent, stabilizer; relative to the dry pulp quality, the amount of hydrogen peroxide is 4.0%, the amount of sodium hydroxide is 3.0%, the amount of DTPA is 0.1%, and the amount of sodium silicate is 0.5%;
[0037] (4) One-stage high-consistency bleaching of pulp: transport the mixture of material and drug into the high-consistency...
Embodiment 3
[0041] (1) Concentrate unbleached eucalyptus chemical pulp and bamboo pulp with a concentration of 20% (the mass ratio of unbleached eucalyptus chemical pulp and bamboo pulp is 2:1) after washing to obtain concentrated pulp with a concentration of 28%. pulp;
[0042] (2) Extruding and dehydrating the concentrated pulp with a parallel twin-screw extruder at a compression ratio of >3.0 to obtain a high-consistency pulp with a concentration of more than 30%;
[0043] (3) Pump hydrogen peroxide and bleaching aid into the high-concentration slurry at a pressure of 1.5 MPa at the extruding part of the parallel twin-screw press to obtain a mixture of ingredients and chemicals; the bleaching solution It is a solution of hydrogen peroxide; bleaching aids include sodium hydroxide, chelating agent, and stabilizer; relative to the dry pulp quality, the amount of hydrogen peroxide is 4.0%, the amount of sodium hydroxide is 3.0%, the amount of DTPA is 0.1%, silicon Sodium acid consumption is...
PUM
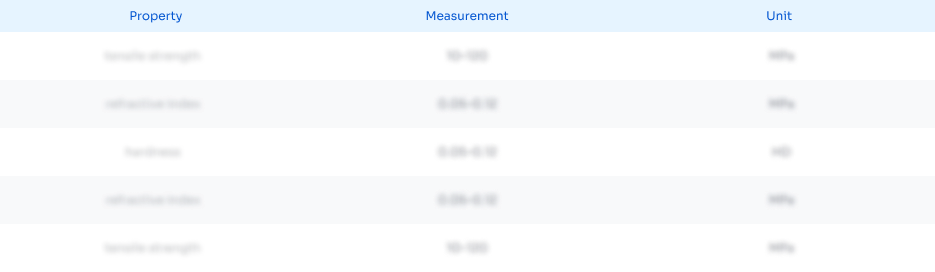
Abstract
Description
Claims
Application Information

- R&D
- Intellectual Property
- Life Sciences
- Materials
- Tech Scout
- Unparalleled Data Quality
- Higher Quality Content
- 60% Fewer Hallucinations
Browse by: Latest US Patents, China's latest patents, Technical Efficacy Thesaurus, Application Domain, Technology Topic, Popular Technical Reports.
© 2025 PatSnap. All rights reserved.Legal|Privacy policy|Modern Slavery Act Transparency Statement|Sitemap|About US| Contact US: help@patsnap.com