Preparation technology of propylene oxide
A technology for propylene oxide and a preparation process, which is applied in the field of preparation technology of propylene oxide, can solve the problems of difficult to build small and medium-sized devices, high requirements for raw materials, and many varieties of raw materials, and achieves energy saving, high selectivity, and single product. Effect
- Summary
- Abstract
- Description
- Claims
- Application Information
AI Technical Summary
Problems solved by technology
Method used
Image
Examples
Embodiment 1
[0037] (1) Chloroalcoholization process: chlorine gas, propylene, and industrial water are put into the bottom of the tubular reactor at a mass ratio of 13:30:20, and chloroalcoholization reaction occurs in the tubular reactor to generate an aqueous solution of monochloropropanol;
[0038] (2) Complexation extraction process: the aqueous solution of monochloropropanol is pumped into the top of the extraction tower, and the complexation extraction agent (anisole, toluene, dimethylacetamide, by mass ratio is 1:2:4) Enter from the middle and lower part of the tower, extract monochloropropanol solution by complexation, take out the water phase from the bottom of the tower, and return to the chloroalcoholization process as industrial water;
[0039] (3) Saponification process: pump the monochloropropanol solution extracted by complexation and 10 parts by mass of sodium hydroxide solution into the saponification reactor, heat up to 102°C, and saponification reaction occurs to generat...
Embodiment 2
[0044] Compared with Example 1, chlorine, propylene, and industrial water required for the chloroalcoholization process in the present embodiment are 20:37:31 by mass ratio; trioctylamine, kerosene, and 200# solvent oil are 2:3 by mass ratio : 5; Carrying out the required sodium hydroxide electrolyte mass fraction of saponification reaction is 12 parts, is warming up to 104 ℃; In saponification waste water, sodium chloride content is 13%, is 26% through evaporation concentration heavy saturated sodium chloride content. The rest of the process and equipment used are the same as those in Embodiment 1, and will not be repeated here.
Embodiment 3
[0046]Compared with Example 1, the chlorine, propylene, and industrial water required for the chloroalcoholization process in the present embodiment are 29:45:35 by mass ratio; methylene chloride, xylene, and isooctyl alcohol are 3:4 by mass ratio : 6; Carrying out the required sodium hydroxide electrolyte mass fraction of saponification reaction is 15 parts, is warming up to 105 ℃; Sodium chloride content is 23% in the saponification waste water, through evaporative concentration heavy saturation, sodium chloride content is 28% . The rest of the process and equipment used are the same as those in Embodiment 1, and will not be described again.
PUM
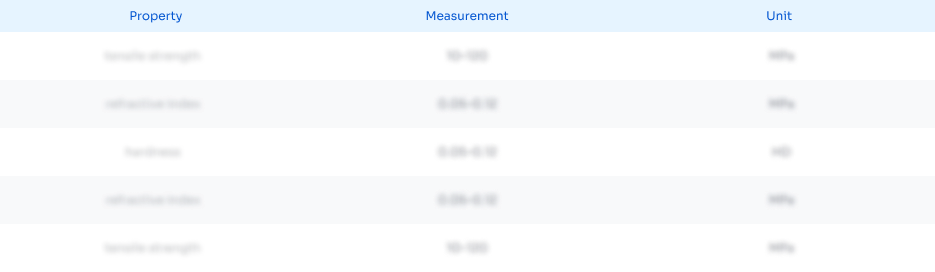
Abstract
Description
Claims
Application Information

- Generate Ideas
- Intellectual Property
- Life Sciences
- Materials
- Tech Scout
- Unparalleled Data Quality
- Higher Quality Content
- 60% Fewer Hallucinations
Browse by: Latest US Patents, China's latest patents, Technical Efficacy Thesaurus, Application Domain, Technology Topic, Popular Technical Reports.
© 2025 PatSnap. All rights reserved.Legal|Privacy policy|Modern Slavery Act Transparency Statement|Sitemap|About US| Contact US: help@patsnap.com