Dry-grinding and dry-separation method of magnetite
A dry separation method and magnetite technology, applied in chemical instruments and methods, solid separation, separating solids from solids with air flow, etc., can solve high tailings disposal costs, high steel consumption of ball mills, and huge maintenance costs and other problems, to achieve the effect of saving money, occupying a small area, and low production cost
- Summary
- Abstract
- Description
- Claims
- Application Information
AI Technical Summary
Problems solved by technology
Method used
Image
Examples
Embodiment 1
[0021] Embodiment 1: as Figure 2-3 As shown, a certain thalassemia magnetite in Inner Mongolia has a total iron content of 11.5% and a magnetic iron content of 6.8%. The crusher is medium crushed, the ore discharge port of the cone crusher is controlled at 20mm, and the material under the screen and the medium crushed product are sent to the high pressure roller mill by the belt. The products of the high-pressure roller mill are sent to the dispersing and classifying machine through the hoist for treatment. The rotor speed is controlled to 300r / min, the fan speed is 1200r / min, and the angle adjustment plate is 20° to obtain +3mm coarse grains, -3+0.2mm fine grains and -Three grades of fine powder of 0.2mm, the coarse-grained product returns to the high-pressure roller mill through the hoist, and the fine-grained product passes through the dry magnetic separator with a magnetic field strength of 1200Gs, and about 30% of the fine-grained tailings are thrown away. The final con...
Embodiment 2
[0022] Embodiment 2: as Figure 2-3 As shown, a certain thalassemia magnetite in Xinjiang has a total iron content of 18.6% and a magnetic iron content of 15.3%. The crusher is crushed, and the ore discharge port of the cone crusher is controlled at 30mm. The under-screen material and the crushed product are fed into the high-pressure roller mill by the belt. The products of the high-pressure roller mill are fed into the elevator, and after being processed by the dispersing classifier, the rotor speed is controlled to 350r / min, the fan speed is 1500r / min, and the angle adjustment plate is 15° to obtain +5mm coarse grains and -5+0.5mm fine grains. Granular and -0.5mm fine powder three grades of products, the coarse product returns to the high-pressure roller mill through the elevator, the fine product passes through the dry magnetic separator, the magnetic field strength is 1800Gs, and about 40% of the fine tailings are thrown away. After the tailings are thrown, the concentra...
PUM
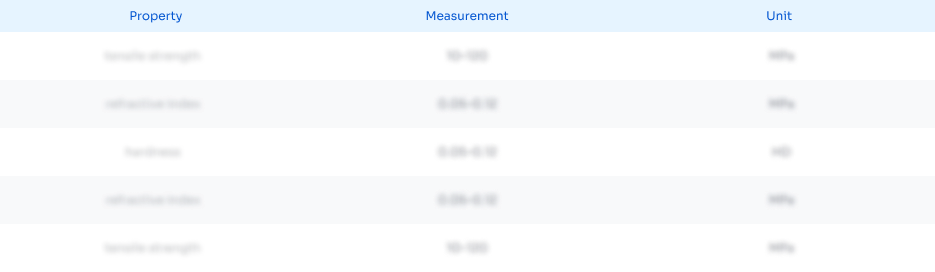
Abstract
Description
Claims
Application Information

- Generate Ideas
- Intellectual Property
- Life Sciences
- Materials
- Tech Scout
- Unparalleled Data Quality
- Higher Quality Content
- 60% Fewer Hallucinations
Browse by: Latest US Patents, China's latest patents, Technical Efficacy Thesaurus, Application Domain, Technology Topic, Popular Technical Reports.
© 2025 PatSnap. All rights reserved.Legal|Privacy policy|Modern Slavery Act Transparency Statement|Sitemap|About US| Contact US: help@patsnap.com