Production method of degradable soybean fiber synthetic leather
A technology of soybean fiber and production method, which is applied in textiles and papermaking, etc., can solve the problem of underutilization of soybean fiber, and achieve the effect of reducing content and reducing environmental pollution.
- Summary
- Abstract
- Description
- Claims
- Application Information
AI Technical Summary
Problems solved by technology
Method used
Image
Examples
Embodiment 1
[0026] Such as figure 1 , figure 2 , image 3 As shown, the soybean fiber with excellent physical properties is selected, and the blending ratio of 30% soybean fiber, 30% nylon fiber and 40% polyester fiber is mixed, and then the soybean fiber is obtained by carding, stacking, acupuncture and shaping. Fiber non-woven fabric; Secondly, according to the wet impregnation method, 100 parts by weight of PU resin, 400 parts by weight of DMF, 2 parts by weight of anionic surfactant, 1 part by weight of nonionic surfactant, and the proportioning of 10 parts by weight of color paste are made into wet PU mixed solution for impregnation, 100 parts by weight of PU resin for wet coating, 40 parts by weight of DMF, 2 parts by weight of anionic surfactant, 1 part by weight of nonionic surfactant, and 10 parts by weight of color paste to make wet PU mixed solution for method coating, the prepared PU mixed solution for wet impregnation and PU mixed solution for wet coating respectively with...
Embodiment 2
[0028] Such as figure 1 , figure 2 , image 3 As shown, the soybean fiber with excellent physical properties is selected, mixed with 20% soybean fiber, 20% nylon fiber, and 60% polyester fiber, and then the soybean fiber is obtained by carding, stacking, acupuncture, and shaping. Fiber non-woven fabric; Secondly, according to the wet impregnation method, 100 parts by weight of PU resin, 300 parts by weight of DMF, 1 part by weight of anionic surfactant, 0.5 part by weight of nonionic surfactant, and the proportioning of 8 parts by weight of color paste are made into wet PU mixed liquid for impregnation, 100 parts by weight of PU resin for wet coating, 30 parts by weight of DMF, 1 part by weight of anionic surfactant, 0.5 part by weight of nonionic surfactant, and 8 parts by weight of color paste to make wet The PU mixed solution for method coating, the prepared PU mixed solution for wet impregnation and the PU mixed solution for wet coating are respectively consumed at a co...
Embodiment 3
[0030] Such as figure 1 , figure 2 , image 3 As shown, select soybean fiber with excellent physical properties, blend cotton at a mixing ratio of 30% soybean fiber, 20% nylon fiber, and 50% polyester fiber, and then obtain soybean fiber through carding, stacking, acupuncture, and shaping. Fiber non-woven fabric; Secondly, according to the wet impregnation with 100 parts by weight of PU resin, DMF500 parts by weight, 3 parts by weight of anionic surfactant, 2 parts by weight of nonionic surfactant, the proportioning of 12 parts by weight of color paste is made wet 100 parts by weight of PU resin for wet coating, 50 parts by weight of DMF, 3 parts by weight of anionic surfactant, 2 parts by weight of nonionic surfactant, and 12 parts by weight of color paste to make wet The PU mixed solution for method coating, the prepared PU mixed solution for wet impregnation and the PU mixed solution for wet coating were impregnated and coated on the soybean fiber without consuming 500g / ...
PUM
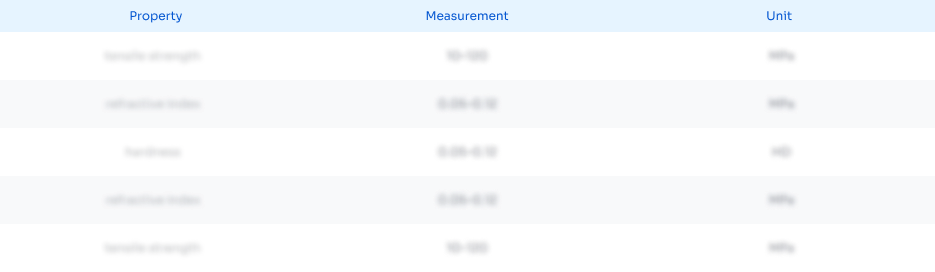
Abstract
Description
Claims
Application Information

- R&D
- Intellectual Property
- Life Sciences
- Materials
- Tech Scout
- Unparalleled Data Quality
- Higher Quality Content
- 60% Fewer Hallucinations
Browse by: Latest US Patents, China's latest patents, Technical Efficacy Thesaurus, Application Domain, Technology Topic, Popular Technical Reports.
© 2025 PatSnap. All rights reserved.Legal|Privacy policy|Modern Slavery Act Transparency Statement|Sitemap|About US| Contact US: help@patsnap.com