High-temperature solutionizing softening process for fine crystalline stainless steel pipe
A stainless steel tube, high-temperature softening technology, applied in the direction of manufacturing tools, furnaces, heat treatment equipment, etc., can solve the problems of loss, heavy workload, and many grinding steps, so as to reduce material loss, reduce follow-up processes, and improve work efficiency effect
- Summary
- Abstract
- Description
- Claims
- Application Information
AI Technical Summary
Problems solved by technology
Method used
Image
Examples
Embodiment 1
[0019] Embodiment 1 High-temperature softening process of fine-grained austenitic stainless steel pipe
[0020] When softening at high temperature, one end of the stainless steel tube is closed with a matching stainless steel cover, and the other end is filled with protective argon gas. After the inflation is completed, the other end is also closed with a matching stainless steel cover. The heat preservation temperature for high temperature softening is controlled at 1200°C-1280°C, and the heat preservation time for high temperature softening is ≥3.0min / mm (pipe wall thickness). During the heating process, there is a gap between the stainless steel tubes to ensure that they do not touch each other
Embodiment 2
[0021] Embodiment 2 compares the amount of thinning of the fine-grained austenitic stainless steel tube wall thickness prepared by different process conditions
[0022] Table 1 TP347HFG 63.5*4 prepared under different process conditions
[0023]
[0024]
[0025] Table 2 S30432 45*11 prepared under different process conditions
[0026]
[0027] Table 3 S30432 50.8*3.5 prepared under different process conditions
[0028]
[0029] The data in Table 1 and Table 2 show that when the protective gas is filled at high temperature softening, the amount of wall thickness reduction is greatly reduced, indicating that the oxidation of the inner wall of the steel pipe is reduced; controlling the heat preservation temperature can also further reduce oxidation and reduce the amount of wall thickness reduction.
[0030] Due to the reduction of oxidation, the production of steel pipes of the same specification can save raw materials. Calculated by using 350 tons of S30432 for a 6...
PUM
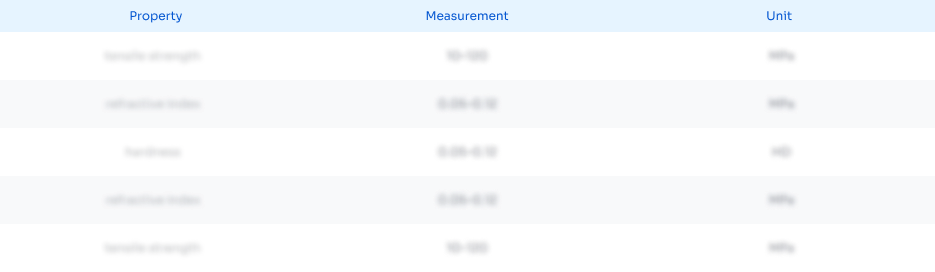
Abstract
Description
Claims
Application Information

- R&D
- Intellectual Property
- Life Sciences
- Materials
- Tech Scout
- Unparalleled Data Quality
- Higher Quality Content
- 60% Fewer Hallucinations
Browse by: Latest US Patents, China's latest patents, Technical Efficacy Thesaurus, Application Domain, Technology Topic, Popular Technical Reports.
© 2025 PatSnap. All rights reserved.Legal|Privacy policy|Modern Slavery Act Transparency Statement|Sitemap|About US| Contact US: help@patsnap.com