Preparation method of copper alloy for high-power LED (light emitting diode) phase-transition internal/external heat dissipators
A high-power, phase-change technology, used in lighting and heating equipment, semiconductor devices of light-emitting elements, cooling/heating devices for lighting devices, etc.
- Summary
- Abstract
- Description
- Claims
- Application Information
AI Technical Summary
Problems solved by technology
Method used
Examples
Embodiment 1
[0023] Embodiment 1: A kind of preparation method of copper alloy for high-power LED phase change type internal and external heat sink, comprises the following steps:
[0024] The first step is to determine the maximum allowable temperature of high-power LED;
[0025] In the second step, according to the maximum temperature allowed by high-power LEDs, the phase transition temperature range of the copper-based alloy determined is: 35°C-100°C;
[0026] The third step is based on the phase transition temperature determined in the second step, and then determines the weight percentage of alloying elements according to the formula Ms (°C)=2112-56.5*(wt%Zn)-153.7*(wt%X);
[0027] The fourth step is to smelt the sample according to the determined composition ratio;
[0028] The fifth step is to keep the smelted sample at 840°C for 30 minutes, and then keep it in boiling water at 100°C for 30 minutes;
[0029] The sixth step is to use a differential thermal analyzer to test whether ...
Embodiment 2
[0036] Embodiment 2: A kind of preparation method of high-power LED phase change type copper alloy for internal and external heat sink, comprises the following steps:
[0037] The first step is to determine the maximum allowable temperature of high-power LED;
[0038] In the second step, according to the maximum allowable temperature of high-power LEDs, the phase transition temperature range of copper-based alloys determined is: 40°C;
[0039] The third step is based on the phase transition temperature determined in the second step, and then determines the weight percentage of alloying elements according to the formula Ms (°C)=2112-56.5*(wt%Zn)-153.7*(wt%X);
[0040] The fourth step is to smelt the sample according to the determined composition ratio;
[0041] The fifth step is to keep the smelted sample at 835°C for 28 minutes, and then keep it in boiling water at 100°C for 28 minutes;
[0042] The sixth step is to test and verify whether the phase transition point is consi...
Embodiment 3
[0049] Embodiment 3: A kind of preparation method of copper alloy for high-power LED phase change type internal and external heat sink, comprises the following steps:
[0050] The first step is to determine the maximum allowable temperature of high-power LED;
[0051] In the second step, according to the maximum temperature allowed by the high-power LED, the phase transition temperature range of the copper-based alloy is determined as: 50°C;
[0052] The third step is based on the phase transition temperature determined in the second step, and then determines the weight percentage of alloying elements according to the formula Ms (°C)=2112-56.5*(wt%Zn)-153.7*(wt%X);
[0053] The fourth step is to smelt the sample according to the determined composition ratio;
[0054] The fifth step is to keep the smelted sample at 845°C for 32 minutes, and then keep it in boiling water at 100°C for 32 minutes;
[0055] The sixth step is to use a differential thermal analyzer to test whether ...
PUM
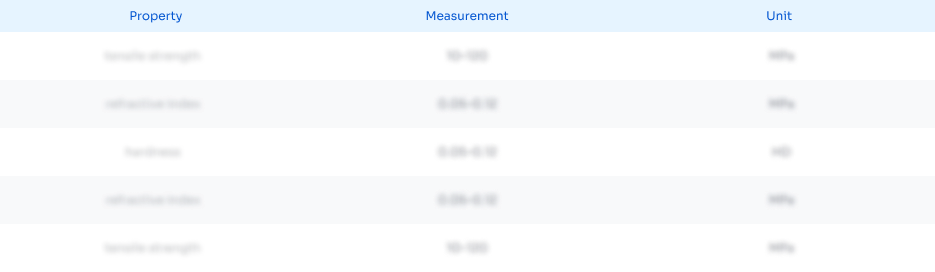
Abstract
Description
Claims
Application Information

- R&D Engineer
- R&D Manager
- IP Professional
- Industry Leading Data Capabilities
- Powerful AI technology
- Patent DNA Extraction
Browse by: Latest US Patents, China's latest patents, Technical Efficacy Thesaurus, Application Domain, Technology Topic, Popular Technical Reports.
© 2024 PatSnap. All rights reserved.Legal|Privacy policy|Modern Slavery Act Transparency Statement|Sitemap|About US| Contact US: help@patsnap.com