Rock drilling machine and axial bearing module
A technology for axial bearings and rock drilling machines, which is applied in the field of rock drilling machines, can solve the problems of difficult assembly and replacement of axial bearings, complicated maintenance, strain, etc., and achieves the effects of facilitating disassembly and installation, light structure, and small size
- Summary
- Abstract
- Description
- Claims
- Application Information
AI Technical Summary
Problems solved by technology
Method used
Image
Examples
Embodiment Construction
[0041] figure 1 A rock drilling unit 1 is shown which may be arranged on a drill boom 2 or the like of a rock drilling rig. The rock drilling unit 1 may comprise a feed beam 3 on which a rock drilling machine 5 is arranged and moved by means of a feed device 4 . The rock drilling machine 5 can be fastened to the carriage 36 and can be moved in the striking direction A and in the returning direction B. As shown in FIG. Furthermore, the rock drilling machine 5 comprises a percussion device 6 for generating a percussion pulse on the drill shank 7 and passing the percussion pulse further through the tool 8 to the rock 9 . Tool 8 may include one or more drill rods and drill bits. Alternatively, the tool 8 may be a one-piece drill rod, in which case a machine component like the drill shank 7 may be considered to be fixedly connected to its end on the rock drilling machine side. Therefore, in this patent application, a drill shank may also refer to the rear end of a one-piece dril...
PUM
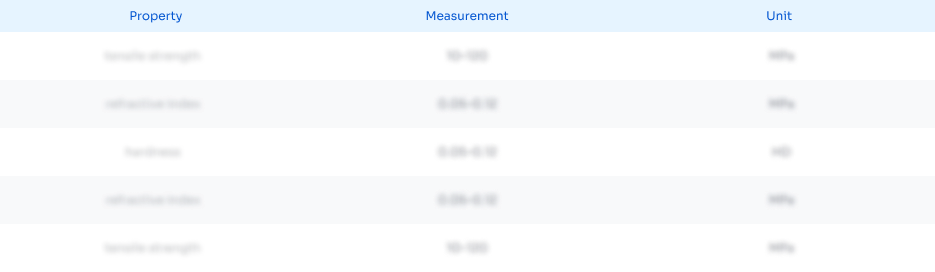
Abstract
Description
Claims
Application Information

- Generate Ideas
- Intellectual Property
- Life Sciences
- Materials
- Tech Scout
- Unparalleled Data Quality
- Higher Quality Content
- 60% Fewer Hallucinations
Browse by: Latest US Patents, China's latest patents, Technical Efficacy Thesaurus, Application Domain, Technology Topic, Popular Technical Reports.
© 2025 PatSnap. All rights reserved.Legal|Privacy policy|Modern Slavery Act Transparency Statement|Sitemap|About US| Contact US: help@patsnap.com