Method for producing high-purity anhydrous zinc chloride
A technology of anhydrous zinc chloride and its production method, which is applied in the direction of improving process efficiency, etc., can solve the problems of high cost and large investment, and achieve the effects of low corrosion, low investment and simple reaction process
- Summary
- Abstract
- Description
- Claims
- Application Information
AI Technical Summary
Problems solved by technology
Method used
Image
Examples
Embodiment 1
[0042] Zinc oxide soot, a by-product of lead smelting in a factory, material composition (%): Zn 42.43, Pb 12.54, Cu 0.04, Cd 0.58, In 0.0226, S 2.8, Cl 0.16, F 0.025, As 0.36, Sb 0.048.
[0043] Newly configured NH 4 Cl-NH 3 The solution is a leaching agent, containing Zn 2+ 0g / L, NH 4 Cl 5.0mol / L, NH 3 3.0mol / L, the solid-liquid ratio is 250g / L, zinc is leached from sub-zinc oxide soot at room temperature, the leaching time is 2.5h, and the leaching rate of zinc during the leaching process is 90.78%.
[0044] Leaching solution composition (g / L): Zn 2+ 96.29, Cu 2+ 0.09, Ni 2+ 0.18, Cd 2+ 1.35, Pb 2+ 0.058. The theoretical consumption of zinc powder is 110g / L, two-stage countercurrent purification at room temperature, adding 3 times the theoretical consumption of zinc powder to replace Cu, Cd, Ni, Co, Pb, etc.
[0045] The resulting Zn(II)-NH 3 -NH 4 Cl solution, neutralize the NH in the solution with 35% hydrochloric acid 3 , control the molar ratio of ammonia a...
Embodiment 2
[0047] Sub-zinc oxide soot obtained by volatilization of low-grade zinc oxide ore in a factory, material composition (%): Zn 68.25, Pb 2.14, Cu 0.14, Cd 1.26, In 0.0699, S 0.34, Cl 0.08, F 0.052, As 0.24, Sb 0.068 .
[0048] Containing Zn 2+ 15g / L, NH 4 Cl 5.5mol / L, NH 3 The 3.0mol / L solution is used as the leaching agent, and the solid-to-liquid ratio is 150g / L. Zinc is leached from sub-zinc oxide soot at room temperature, and the leaching time is 1.5h. The leaching rate of zinc during the leaching process is 98.27%.
[0049] Leaching solution composition (g / L): Zn 2+ 115.21, Cu 2+ 0.21, Ni 2+ 0.09, Co 2+ 0.007, Cd 2+ 1.96, Pb 2+ 0.064. use. The theoretical consumption of zinc powder is 1.48g / L, two-stage countercurrent purification at room temperature, adding zinc powder twice the theoretical consumption to replace Cu, Cd, Ni, Co, Pb, etc.
[0050] The resulting Zn(II)-NH 3 -NH 4 Cl solution, neutralize the NH in the solution with hydrochloric acid 3 , control ...
Embodiment 3
[0053] Zinc oxide ash produced by a recycling smelter, material composition (%): Zn 74.43, Pb 0.0032, Cu 0.0004, Cd 0.0002, Cl 6.56.
[0054] Containing Zn 2+ 10g / L, NH 4 Cl 4.5mol / L, NH 3 The solution of 3.0mol / L is the leaching agent, and the solid-liquid ratio is 100g / L. Zinc is leached from zinc ash at room temperature, and the leaching time is 0.5h. The leaching rate of zinc during the leaching process is 93.43%. state exists.
PUM
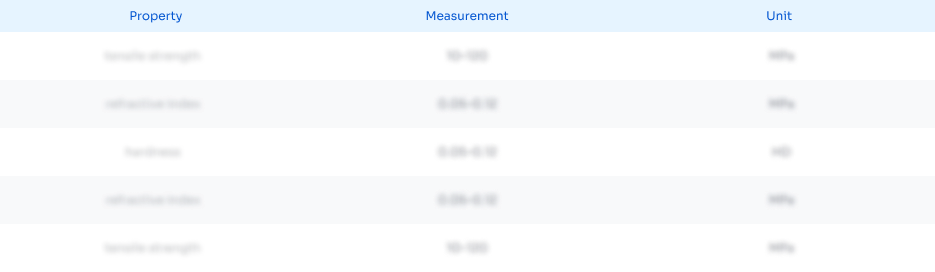
Abstract
Description
Claims
Application Information

- R&D Engineer
- R&D Manager
- IP Professional
- Industry Leading Data Capabilities
- Powerful AI technology
- Patent DNA Extraction
Browse by: Latest US Patents, China's latest patents, Technical Efficacy Thesaurus, Application Domain, Technology Topic, Popular Technical Reports.
© 2024 PatSnap. All rights reserved.Legal|Privacy policy|Modern Slavery Act Transparency Statement|Sitemap|About US| Contact US: help@patsnap.com