Heat-resistant thermoplastic polyurethane elastomer and preparation method thereof
A thermoplastic polyurethane and elastomer technology, applied in the field of polyurethane, can solve the problems of high price of PPDI, high vapor pressure, increased cost, etc., and achieve good comprehensive mechanical properties, good high temperature resistance, and avoid the effect of adding volatilization.
- Summary
- Abstract
- Description
- Claims
- Application Information
AI Technical Summary
Problems solved by technology
Method used
Image
Examples
Embodiment 1
[0036] a) Dehydrate 300g of PCL (PCL-2000) with a number-average molecular weight of 2000 at 100-105°C for 2 hours under a vacuum degree of -0.098--0.01MPa, add 148g of solid TODI, and react at a temperature of 80-85°C , a storage-stable prepolymer with an NCO mass fraction of 7.70% was obtained.
[0037] b) mix 74g 1,4-butanediol, 0.08g catalyst bismuth isooctanoate, 1g antioxidant Irgastab PUR68, 3g ultraviolet light absorber Tinuvin213 and 2g light stabilizer UV-765, and prepolymer with a) Mix in a ratio of 92:8 by mass.
[0038] c) The mixture in b) was vacuumed and defoamed, then poured into a mold at 180°C for 15 minutes for demoulding, and the semi-finished product after demoulding was placed in an oven at 120°C and aged for 24 hours to obtain a finished product. The main performance indicators are shown in Table 1.
Embodiment 2
[0040] a) Dehydrate 300g of PCL (PCL-1000) with a number-average molecular weight of 1000 at 100-105°C and a vacuum of -0.098--0.01MPa for 2 hours, add solid 123.7g TODI, and react at a temperature of 80-85°C , resulting in a storage-stable prepolymer with a mass fraction of NCO of 6.30%.
[0041] b) 124g of HQEE, 1g of antioxidant 1010, 3g of UV absorber Tinuvin213 and 2g of light stabilizer UV-765 were evenly mixed, and mixed with the prepolymer in a) at a mass ratio of 87:13.
[0042] c) The mixture in b) was defoamed in vacuum and poured into a mold at 180°C for 15 minutes for demoulding, and the semi-finished product after demoulding was placed in an oven at 100°C and aged for 20 hours to obtain a finished product. The main performance indicators are shown in Table 1.
Embodiment 3
[0044] a) Dehydrate 300g of PTMG (PTMG-2000) with a number-average molecular weight of 2000 at 100-105°C, vacuum degree -0.098-0.01MPa for 2h, add 103.2g of solid TODI, and carry out at a temperature of 80-85°C reaction to generate a storage-stable prepolymer with a mass fraction of NCO of 5.00%.
[0045] b) Mix 37g 1,4-butanediol, 0.02g catalyst bismuth carboxylate, 1g antioxidant 1135, 3g UV absorber Tinuvin571 and 2g light stabilizer UV-765, and mix with the prepolymer of a) Mix according to the ratio of mass ratio 95.7:4.3.
[0046] c) The mixture in b) was defoamed in vacuum and poured into a mold at 160°C for 15 minutes for demoulding, and the semi-finished product after demoulding was placed in an oven at 110°C and aged for 24 hours to obtain the finished product. The main performance indicators are shown in Table 1.
PUM
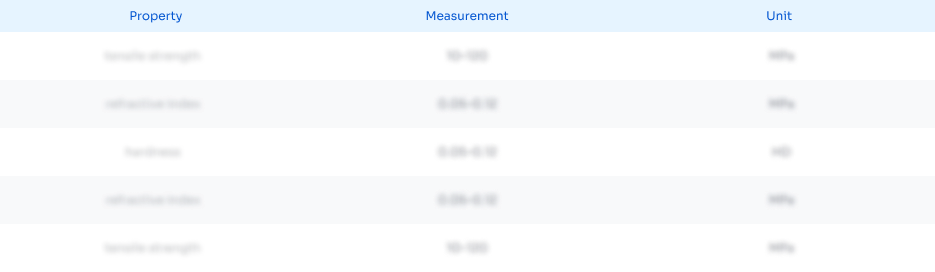
Abstract
Description
Claims
Application Information

- Generate Ideas
- Intellectual Property
- Life Sciences
- Materials
- Tech Scout
- Unparalleled Data Quality
- Higher Quality Content
- 60% Fewer Hallucinations
Browse by: Latest US Patents, China's latest patents, Technical Efficacy Thesaurus, Application Domain, Technology Topic, Popular Technical Reports.
© 2025 PatSnap. All rights reserved.Legal|Privacy policy|Modern Slavery Act Transparency Statement|Sitemap|About US| Contact US: help@patsnap.com