Dry-mixed masonry mortar for industrial dust
A dry-mixed mortar and dust technology, which is applied in the field of industrial dust dry-mixed mortar, can solve the problems of mortar cracking and inability to be applied in the field of dry-mixed mortar production, and achieve the effects of increasing strength, reducing shrinkage and cracking, and reducing volatilization
- Summary
- Abstract
- Description
- Claims
- Application Information
AI Technical Summary
Problems solved by technology
Method used
Image
Examples
Embodiment 1
[0023] Embodiment 1 (interior wall plastering dry-mixed mortar):
[0024] formula:
[0025] Ordinary silicon cement 425#: 9Kg Mining industrial dust: 12Kg
[0026] Machine-made sand: 80Kg (fineness less than 4mm) Composite activator: 0.35Kg
[0027] Composite water retaining agent: 0.08Kg Perlite (40 mesh): 0.1Kg
[0028] The composite activator is: triethanolamine, triisopropanolamine and polycarboxylate water reducer compounded in a weight ratio of 1:1:1.
[0029] The composite water-retaining agent is composed of hydroxypropyl methylcellulose and polyacrylamide in a weight ratio of 3:5.
[0030] Preparation:
[0031] After accurately measuring various raw materials according to the above formula, mix and force mechanical stirring to obtain the target product.
Embodiment 2
[0032] Embodiment 2 (external wall plastering dry-mixed mortar):
[0033] Ordinary silicon cement 425#: 9Kg Mining industrial dust: 12Kg
[0034] Machine-made sand: 80Kg (fineness less than 4mm) Composite activator: 0.35Kg
[0035] Composite water retaining agent: 0.08Kg Perlite (40 mesh): 0.1Kg
[0037] The composite activator is: triethanolamine, triisopropanolamine and polycarboxylate water reducer compounded in a weight ratio of 1:1:1.
[0038] The composite water-retaining agent is composed of hydroxypropyl methylcellulose and polyacrylamide in a weight ratio of 3:5.
[0039] Preparation:
[0040] After accurately measuring various raw materials according to the above formula, mix and force mechanical stirring to obtain the target product.
Embodiment 3
[0041] Embodiment three (interior wall plastering dry-mixed mortar):
[0042] formula:
[0043] Ordinary silicon cement 425#: 10Kg Sand and gravel crushing industrial dust: 15Kg
[0044] Construction waste crushed particles: 74Kg (fineness less than 4mm) Composite activator: 0.4Kg
[0045] Composite water retaining agent: 0.085Kg Microcrystalline paraffin: 0.15Kg
[0046] Fly ash: 1Kg
[0047] The composite activator is: triethanolamine, triisopropanolamine and polycarboxylate water reducer compounded in a weight ratio of 1:1:1.
[0048] The composite water-retaining agent is composed of hydroxypropyl methylcellulose and polyacrylamide in a weight ratio of 3:5.
[0049] Preparation:
[0050] After accurately measuring various raw materials according to the above formula, mix and force mechanical stirring to obtain the target product.
PUM
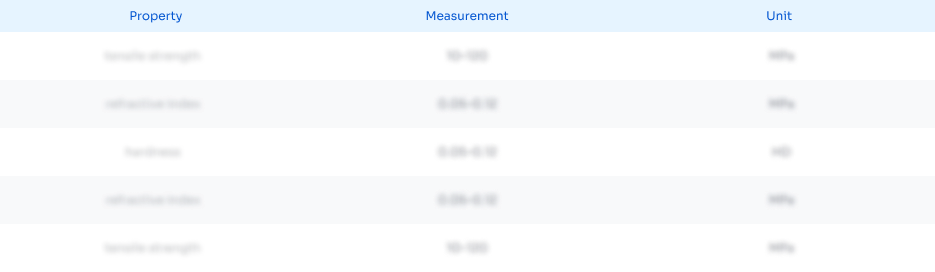
Abstract
Description
Claims
Application Information

- R&D
- Intellectual Property
- Life Sciences
- Materials
- Tech Scout
- Unparalleled Data Quality
- Higher Quality Content
- 60% Fewer Hallucinations
Browse by: Latest US Patents, China's latest patents, Technical Efficacy Thesaurus, Application Domain, Technology Topic, Popular Technical Reports.
© 2025 PatSnap. All rights reserved.Legal|Privacy policy|Modern Slavery Act Transparency Statement|Sitemap|About US| Contact US: help@patsnap.com