Chromium plate manufacturing process
A manufacturing process and chrome plate technology, applied in the field of chrome plate manufacturing technology, can solve problems such as chrome plate damage, and achieve the effects of high anti-static discharge damage and good pattern effect.
- Summary
- Abstract
- Description
- Claims
- Application Information
AI Technical Summary
Problems solved by technology
Method used
Image
Examples
Embodiment Construction
[0016] see figure 1 , is a schematic flow diagram of a preferred embodiment of the chrome plate manufacturing process of the present invention.
[0017] The chrome plate manufacturing process of the present invention comprises:
[0018] Step a, cleaning and drying the glass substrate;
[0019] In step b, the glass substrate is sputter-coated with a light-shielding layer in a vacuum chamber, wherein the transmission rate of the glass substrate is 0.25 m / min to 0.35 m / min, and the volume flow rate of argon gas is 80 ml / min to 200 m / min Standard condition ml / min, nitrogen volume flow rate is 180 standard condition ml / min to 320 standard condition ml / min, sputtering voltage is 250 volts to 650 volts, sputtering current is 1.2 amps to 3.5 amps;
[0020] Step c, return through the rotary chamber and sputter-coat the glass substrate with a light-absorbing layer, wherein the transmission rate of the glass substrate is 0.25 m / min to 0.35 m / min, and the volume flow rate of argon gas i...
PUM
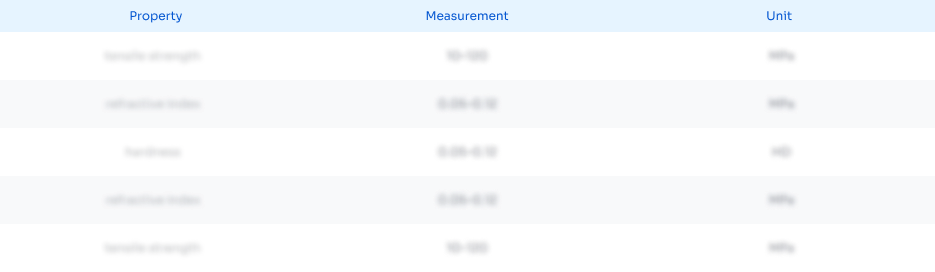
Abstract
Description
Claims
Application Information

- R&D
- Intellectual Property
- Life Sciences
- Materials
- Tech Scout
- Unparalleled Data Quality
- Higher Quality Content
- 60% Fewer Hallucinations
Browse by: Latest US Patents, China's latest patents, Technical Efficacy Thesaurus, Application Domain, Technology Topic, Popular Technical Reports.
© 2025 PatSnap. All rights reserved.Legal|Privacy policy|Modern Slavery Act Transparency Statement|Sitemap|About US| Contact US: help@patsnap.com