Method for manufacturing screen sealing panel, screen sealing panel and television
A production method and screen panel technology, which is applied in the direction of TV, color TV, color TV parts, etc., can solve the problems of high mass production cost, poor surface quality of screen sealing panel, etc., achieve low mass production cost, improve quality, Anti-scratch effect
- Summary
- Abstract
- Description
- Claims
- Application Information
AI Technical Summary
Problems solved by technology
Method used
Image
Examples
Embodiment 1
[0035] figure 1 A flow chart of the method for manufacturing the screen sealing panel provided by the first embodiment of the present invention is shown, and for convenience of description, only parts related to this embodiment are shown.
[0036] The manufacturing method of the screen sealing panel comprises the following steps:
[0037] In step S101, an injection molded part of the screen sealing panel is manufactured by using an IMR molding process.
[0038] In step S102, UV curing treatment is performed on the outer surface of the injection molded part of the screen sealing panel.
[0039] In step S103, anti-fog and anti-static treatment is performed on the inner surface of the injection molded part of the screen-sealing panel to obtain the screen-sealing panel.
[0040] The embodiment of the present invention uses the IMR molding process to make the injection molded part of the sealing panel, and realizes the effect of three-dimensional molding and appearance decoration...
Embodiment 2
[0044] figure 2 It shows a schematic diagram of the front view structure of the screen sealing panel to be produced provided by the second embodiment of the present invention, image 3 It shows a side view structural schematic diagram of the screen sealing panel to be produced provided by the second embodiment of the present invention, Figure 4 It shows a schematic diagram of the printing layer provided by the second embodiment of the present invention, which is as large as the screen sealing panel to be made (the corresponding LOGO, product model, touch key logo and other patterns are omitted in the figure), Figure 5 A schematic structural view of the printed layer of the IMR membrane provided by the second embodiment of the present invention is shown, Figure 6 A schematic structural diagram of the IMR diaphragm provided by the second embodiment of the present invention is shown, and for convenience of description, only parts related to this embodiment are shown.
[004...
Embodiment 3
[0057] Figure 7 A schematic structural view of the injection molding device provided by the third embodiment of the present invention is shown, Figure 8 A schematic diagram of the gate structure of the injection molding device provided by the third embodiment of the present invention is shown, Figure 9 A schematic diagram of the working state of the injection molding device provided by the third embodiment of the present invention is shown, and for the convenience of description, only the parts related to this embodiment are shown.
[0058] The embodiment of the present invention further elaborates the step of "using an IMR injection mold and an injection molding machine to inject and form an injection molded part of a screen sealing panel".
[0059] combined with Figure 7 , In the embodiment of the present invention, the IMR injection mold is preferably an IMR steam mold, including a movable mold 71 and a fixed mold 72, the movable mold 71 is fixed on the movable templa...
PUM
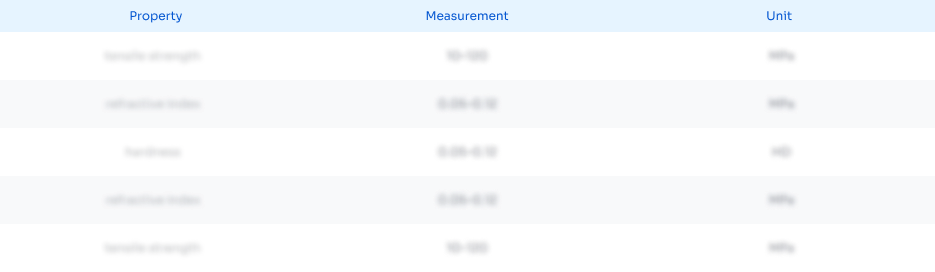
Abstract
Description
Claims
Application Information

- Generate Ideas
- Intellectual Property
- Life Sciences
- Materials
- Tech Scout
- Unparalleled Data Quality
- Higher Quality Content
- 60% Fewer Hallucinations
Browse by: Latest US Patents, China's latest patents, Technical Efficacy Thesaurus, Application Domain, Technology Topic, Popular Technical Reports.
© 2025 PatSnap. All rights reserved.Legal|Privacy policy|Modern Slavery Act Transparency Statement|Sitemap|About US| Contact US: help@patsnap.com