Decumbent corydalis tuber vacuum freeze drying process and preparation process for decumbent corydalis tuber powder
A technology of drying process and preparation process, which is applied in the directions of medical preparations containing active ingredients, plant/algae/fungus/moss ingredients, plant raw materials, etc. Master the dosage and other issues to achieve the effect of retaining the efficacy and its active ingredients, promoting the modernization of traditional Chinese medicine, and saving traditional Chinese medicine resources
- Summary
- Abstract
- Description
- Claims
- Application Information
AI Technical Summary
Problems solved by technology
Method used
Image
Examples
Embodiment 1
[0028] Adopt vacuum freeze dryer to carry out summer without vacuum freeze-drying.
[0029] Such as figure 1 As shown, select fresh summer free raw materials, take out inferior quality and impurities, remove fibrous roots, and wash at a high concentration; pre-dry summer free to a water content of 90%, and then pack them into trays. The weight of the trays is 14kg / m 2 , thickness 2.5cm, pre-freeze at -30°C after gradually cooling down for 2 hours; then vacuumize the system until the absolute pressure of the system is 65Pa, start heating to 40°C-70°C, sublimation and drying for 18 hours; then keep the material temperature at 35°C, Make the water content below 2% before discharge.
[0030] Such as figure 2 As shown, after the above-mentioned steps, Xia Tian has passed through the grinding powder, and after passing through a 100-mesh sieve, the physical wall is broken. In a sealed and dry state, two supersonic airflows are used to impact the Xia Tian powder, and the wall break...
Embodiment 2
[0033]Adopt vacuum freeze dryer to carry out summer without vacuum freeze-drying.
[0034] Select summer free raw materials, take out inferior quality and impurities, remove fibrous roots, and wash at a high concentration; pre-dry summer free to a water content of 80%, and then pack them into trays. The weight of the trays is 12kg / m 2 , thickness 2cm, pre-freeze at -40°C after gradually cooling down for 2 hours; then vacuumize the system until the absolute pressure of the system is 70Pa, start heating to 50°C-70°C, sublimation and drying for 20 hours; then keep the material temperature at 40°C, so that Discharge after the water content reaches below 3%.
[0035] After the above-mentioned steps, the summer powder is crushed through a 100-mesh sieve, and the physical wall is broken. In a sealed and dry state, two supersonic airflows are used to impact the summer powder. The wall breaking rate reaches 98%. After the wall is broken, it will be dehumidified and packaged in a const...
Embodiment 3
[0037] Adopt vacuum freeze dryer to carry out summer without vacuum freeze-drying.
[0038] Select summer free raw materials, take out inferior quality and impurities, remove fibrous roots, and wash at a high concentration; pre-dry summer free to a water content of 70%, and then pack them into trays, and the weight of the trays is 10kg / m 2 , thickness 2cm, pre-freeze at -60°C after gradually cooling down for 3 hours; then vacuumize the system until the absolute pressure of the system is 75Pa, start heating to 60°C-70°C, sublimation and drying for 22 hours; then keep the material temperature at 45°C, so that Discharge after the water content reaches below 3%.
[0039] After the above-mentioned steps, the summer powder is crushed through a 100-mesh sieve, and the physical wall is broken. In a sealed and dry state, two supersonic airflows are used to impact the summer powder. The wall breaking rate reaches 98%. After the wall is broken, it will be dehumidified and packaged in a ...
PUM
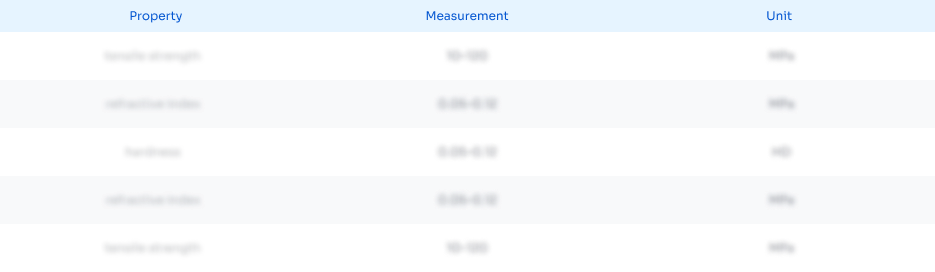
Abstract
Description
Claims
Application Information

- Generate Ideas
- Intellectual Property
- Life Sciences
- Materials
- Tech Scout
- Unparalleled Data Quality
- Higher Quality Content
- 60% Fewer Hallucinations
Browse by: Latest US Patents, China's latest patents, Technical Efficacy Thesaurus, Application Domain, Technology Topic, Popular Technical Reports.
© 2025 PatSnap. All rights reserved.Legal|Privacy policy|Modern Slavery Act Transparency Statement|Sitemap|About US| Contact US: help@patsnap.com