Carbon fiber reinforced boron nitride composite and preparation method thereof
A composite material and carbon fiber technology, which is applied in the field of precursor-converted carbon fiber reinforced boron nitride composite material and its preparation, and achieves the effects of simple preparation process, high ceramic conversion rate and good high temperature resistance performance.
- Summary
- Abstract
- Description
- Claims
- Application Information
AI Technical Summary
Problems solved by technology
Method used
Image
Examples
Embodiment 1
[0020] Select T300 carbon fiber and weave it into a three-dimensional four-way structure three-dimensional fabric, in which the fiber volume fraction is 33%;
[0021] Put the fabric in a sealable container, vacuumize it, suck the liquid borazine into the container, and soak for 1 hour; the final impregnation amount is based on the liquid level being higher than the fabric;
[0022] Then place it in a closed autoclave with a pressure of 4MPa, heat it to 80°C under the protection of an inert atmosphere, and keep it warm for 55 hours to make the liquid borazine cross-linked and solidified;
[0023] Put the cured product in a vacuum cracking furnace at 1200°C, and keep it warm for 2 hours;
[0024] The above impregnation-crosslinking-cracking process was repeated for 3 cycles to obtain carbon fiber reinforced boron nitride composite material.
[0025] The performance of the three-dimensional four-way carbon fiber (T300) fabric reinforced boron nitride composite material prepared ...
Embodiment 2
[0028] a. Select T300 carbon fiber and weave it into a three-dimensional fabric with a 2.5-dimensional structure (between two-dimensional and three-dimensional), in which the fiber volume fraction is 40%.
[0029] b. Fully immerse borazine into the carbon fiber fabric under vacuum conditions, then place it in a closed autoclave (pressure 7MPa), heat it to 100°C under the protection of an inert atmosphere, and keep it warm for 35 hours to make the liquid borazine Joint curing;
[0030] a. Select T300 carbon fiber and weave it into a three-dimensional fabric with a 2.5D structure, in which the fiber volume fraction is 40%.
[0031] b. Fully immerse the borazine into the carbon fiber fabric under vacuum conditions, then place it in a closed autoclave, heat it to 100°C under the protection of an inert atmosphere, and keep it warm for 35 hours to crosslink and solidify the liquid borazine;
[0032] c. Place the cured product in a vacuum cracking furnace with a cracking temperature...
Embodiment 3
[0035] a. Select T700 carbon fiber and weave it into a three-dimensional five-dimensional fabric with a fiber volume fraction of 30%.
[0036] b. Fully immerse borazine into the carbon fiber fabric under vacuum conditions, then place it in a closed autoclave (pressure 4MPa), heat it to 100°C under the protection of an inert atmosphere, and keep it warm for 35 hours to make the liquid borazine Joint curing;
[0037] c. Place the cured product in a vacuum cracking furnace with a cracking temperature of 1500°C and keep it warm for 1 hour;
[0038] d. Repeat the impregnation-crosslinking-cracking process for 2 cycles to obtain a carbon fiber reinforced boron nitride composite material with relatively high porosity.
PUM
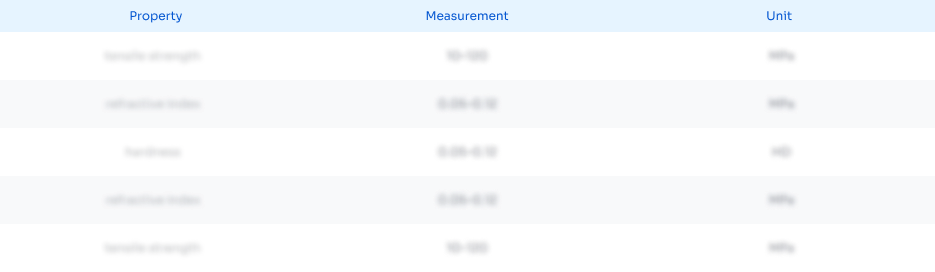
Abstract
Description
Claims
Application Information

- R&D
- Intellectual Property
- Life Sciences
- Materials
- Tech Scout
- Unparalleled Data Quality
- Higher Quality Content
- 60% Fewer Hallucinations
Browse by: Latest US Patents, China's latest patents, Technical Efficacy Thesaurus, Application Domain, Technology Topic, Popular Technical Reports.
© 2025 PatSnap. All rights reserved.Legal|Privacy policy|Modern Slavery Act Transparency Statement|Sitemap|About US| Contact US: help@patsnap.com