Method and system for recovering high-temperature sensible heat of molten blast furnace slag
A technology for blast furnace slag and slag, which is applied in the field of high temperature sensible heat recovery of molten blast furnace slag, can solve the problem of high requirements on equipment processing capacity, temperature resistance and wear resistance and adjustment ability, unfavorable equipment energy consumption and waste heat recovery rate, and recovery of blast furnace slag waste heat. Difficulty and other problems, to achieve the effect of saving drying energy consumption, reducing the power consumption of the circulation system, and the granularity
- Summary
- Abstract
- Description
- Claims
- Application Information
AI Technical Summary
Problems solved by technology
Method used
Image
Examples
Embodiment
[0038] As shown in the figure, the high temperature sensible heat recovery system for molten blast furnace slag consists of blast furnace slag ditch 1, slag hopper 2, slag hopper lifting mechanism 3, rapid cooling unit 4, slow cooling unit 5, cold slag particle circulation unit 6, cyclone dust collector 7, It is composed of waste heat boiler 8, condensing unit 9, circulation fan 10 and pressurization fan 11.
[0039] Specifically, the blast furnace slag ditch 1 is usually a part of the structure of the blast furnace itself, and is a channel for blast furnace slag discharged from the blast furnace. The slag hopper 2 is made of refractory material and holds the liquid high-temperature blast furnace slag flowing out of the blast furnace slag ditch 1; in order to ensure the fluidity of the slag, the slag hopper 2 is equipped with a heating and heat preservation device; in order to reduce the waiting time between two slag discharges, The flow rate of slag treatment is stabilized so...
PUM
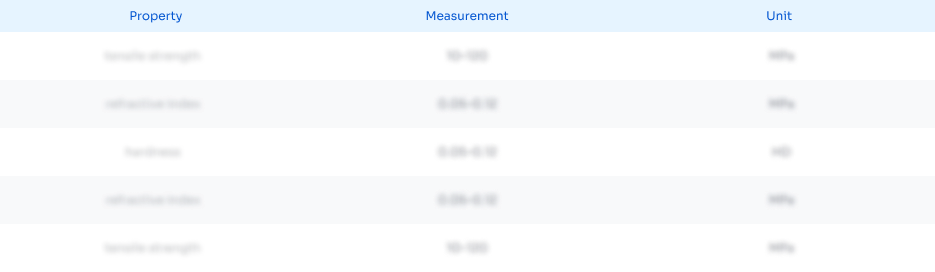
Abstract
Description
Claims
Application Information

- Generate Ideas
- Intellectual Property
- Life Sciences
- Materials
- Tech Scout
- Unparalleled Data Quality
- Higher Quality Content
- 60% Fewer Hallucinations
Browse by: Latest US Patents, China's latest patents, Technical Efficacy Thesaurus, Application Domain, Technology Topic, Popular Technical Reports.
© 2025 PatSnap. All rights reserved.Legal|Privacy policy|Modern Slavery Act Transparency Statement|Sitemap|About US| Contact US: help@patsnap.com