Foaming styrene chloroprene rubber (SCR) and manufacturing method thereof
A foaming rubber and foaming agent technology, which is used in the manufacture of SCR foamed rubber and the field of SCR foamed rubber, can solve problems such as the inability to meet the use requirements of foamed rubber, and achieve good seawater extraction resistance, excellent cold resistance, The effect of uniform and fine closed-cell structure
- Summary
- Abstract
- Description
- Claims
- Application Information
AI Technical Summary
Problems solved by technology
Method used
Image
Examples
Embodiment 1
[0021]The manufacturing steps of SCR foam rubber are as follows: (1) Prepare raw materials according to the following components and weight content: 100 parts of main ingredients, 5 parts of brown ointment, 10 parts of aromatic oil, 20 parts of naphthenic oil, dispersant WB212:1 1 part, foaming agent AC-9: 5 parts, active zinc oxide 4 parts, stearic acid 1 part, highly active magnesium oxide 1 part, sulfur 0.4 part, accelerator DM 0.5 part, accelerator M: 0.2 part, protective wax 1 part, anti-aging agent CPL: 1 part, anti-aging agent ODA: 1 part, and 100 parts of talcum powder; the main material is composed of neoprene, emulsion polystyrene butadiene rubber, polybutadiene rubber and solution polystyrene butadiene rubber. The weight ratio of each component is neoprene: emulsion polystyrene butadiene rubber: polybutadiene rubber: solution polystyrene butadiene rubber = 30:10:20:20.
[0022] (2) Gluing: Put all the main materials, dispersant and one-third of the plasticizer into ...
Embodiment 2
[0031] The manufacturing steps of SCR foam rubber are as follows: (1) Prepare raw materials according to the following components and weight content: 100 parts of main ingredients, 10 parts of brown ointment, 20 parts of aromatic oil, 30 parts of naphthenic oil, dispersant WB42: 2 1 part, foaming agent AC-11: 15 parts, 8 parts of active zinc oxide, 2 parts of stearic acid, 2 parts of highly active magnesium oxide, 1 part of sulfur, accelerator DM: 2 parts, accelerator M: 1 part, protection 2 parts of wax, anti-aging agent CPL: 2 parts, anti-aging agent ODA: 2 parts and 200 parts of calcium carbonate; the main material is composed of neoprene, emulsion polystyrene butadiene rubber, polybutadiene rubber and solution polystyrene butadiene rubber. The weight ratio of each component is neoprene: emulsion polystyrene butadiene rubber: polybutadiene rubber: solution polystyrene butadiene rubber = 30:20:40:30.
[0032] (2) Gluing: Put all the main ingredients, dispersant and one-third...
Embodiment 3
[0041] The manufacturing steps of SCR foam rubber are as follows: (1) Prepare raw materials according to the following components and weight content: 100 parts of main ingredients, 7 parts of brown ointment, 15 parts of aromatic oil, 23 parts of naphthenic oil, and dispersant Deoflow A: 1.5 parts, foaming agent AC3000: 10 parts, active zinc oxide 6 parts, stearic acid 1.5 parts, highly active magnesium oxide 1.5 parts, sulfur 0.7 parts, accelerator DM: 1.2 parts, accelerator M: 0.6 parts, protective wax 1.5 parts, anti-aging agent CPL: 1.5 parts, anti-aging agent ODA: 1.5 parts and clay 150 parts; the main material is composed of neoprene, emulsion polystyrene butadiene rubber, polybutadiene rubber and solution polystyrene butadiene rubber. The parts by weight ratio is neoprene: emulsion polystyrene butadiene rubber: polybutadiene rubber: solution polystyrene butadiene rubber = 30:15:30:25.
[0042] (2) Gluing: Put all the main materials, dispersant and one-third of the plasti...
PUM
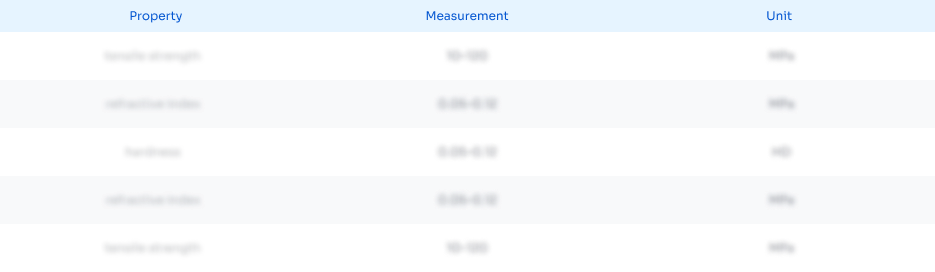
Abstract
Description
Claims
Application Information

- Generate Ideas
- Intellectual Property
- Life Sciences
- Materials
- Tech Scout
- Unparalleled Data Quality
- Higher Quality Content
- 60% Fewer Hallucinations
Browse by: Latest US Patents, China's latest patents, Technical Efficacy Thesaurus, Application Domain, Technology Topic, Popular Technical Reports.
© 2025 PatSnap. All rights reserved.Legal|Privacy policy|Modern Slavery Act Transparency Statement|Sitemap|About US| Contact US: help@patsnap.com