Method for producing luminous organic glass embedded handicraft
A technology of plexiglass and production method, applied in the direction of decorative art, special decorative structure, etc., can solve the problems of aggravating the agglomeration, precipitation and layering of luminous powder, prolonging the polymerization reaction time, affecting product quality, etc.
- Summary
- Abstract
- Description
- Claims
- Application Information
AI Technical Summary
Problems solved by technology
Method used
Examples
Embodiment 1
[0019] Embodiment 1,1) at first add the initiator dibenzoyl peroxide of methyl methacrylate monomer quality 0.3% in methyl methacrylate monomer, stir with magnetic stirrer, after initiator is dissolved completely Use a water bath to heat and prepolymerize at 90°C for 20 minutes until the system becomes viscous with glycerin, stop heating, and cool rapidly to obtain prepolymerization slurry;
[0020] The methyl methacrylate monomer is first washed 4 times with 10% NaOH and then washed 4 times with distilled water until the pH value of the monomer is close to 7, and then washed with anhydrous CaCl 2 Dry for 30 minutes, and finally carry out vacuum distillation.
[0021] 2) Then add 5% of the mass of methyl methacrylate monomer to the 1 / 3 of the prepolymerized slurry prepared in step 1) after water removal, grinding, and sieving until the particle size is 200-400 mesh luminous powder, 1.25% The anti-sedimentation agent silicon dioxide and 0.125% antifoaming agent tetramethoxysil...
Embodiment 2
[0024] Embodiment 2, 1) at first add the initiator azobisisobutyronitrile of methyl methacrylate monomer quality 0.5% in methyl methacrylate monomer, stir with magnetic stirrer, after initiator is completely dissolved Heat in a water bath, prepolymerize at 83°C for 28 minutes until the system becomes viscous with glycerin, stop heating, and cool rapidly to obtain prepolymerization slurry;
[0025] The methyl methacrylate monomer is first washed 3 times with 10% NaOH and then washed 4 times with distilled water until the pH value of the monomer is close to 7, and then washed with anhydrous CaCl 2 Dry for 50 minutes, and finally carry out vacuum distillation.
[0026] 2) Then add 20% of the mass of methyl methacrylate monomer to 2 / 3 of the pre-polymerization slurry prepared in step 1) after water removal, grinding, and sieving until the particle size is 200-400 mesh luminous powder, 5% The anti-precipitation agent sodium lauryl sulfate and 0.5% antifoaming agent simethicone, me...
Embodiment 3
[0029] Embodiment 3, 1) at first add the initiator dibenzoyl peroxide of methyl methacrylate monomer quality 0.4% in methyl methacrylate monomer, stir with magnetic stirrer, after initiator is dissolved completely Heat in a water bath, prepolymerize at 86°C for 23 minutes until the system becomes viscous with glycerin, stop heating, and cool rapidly to obtain prepolymerization slurry;
[0030] The methyl methacrylate monomer is first washed 3 times with 10% NaOH and then washed 4 times with distilled water until the pH value of the monomer is close to 7, and then washed with anhydrous CaCl 2 Dry for 60 minutes, and finally carry out vacuum distillation.
[0031] 2) Then, in 1 / 2 of the prepolymerized slurry prepared in step 1), add 15% of the mass of methyl methacrylate monomer after water removal, grinding, and sieving until the particle size is 200-400 mesh luminous powder, 2.5% The anti-precipitation agent sodium lauryl sulfate and 0.35% antifoaming agent tetramethoxysilane...
PUM
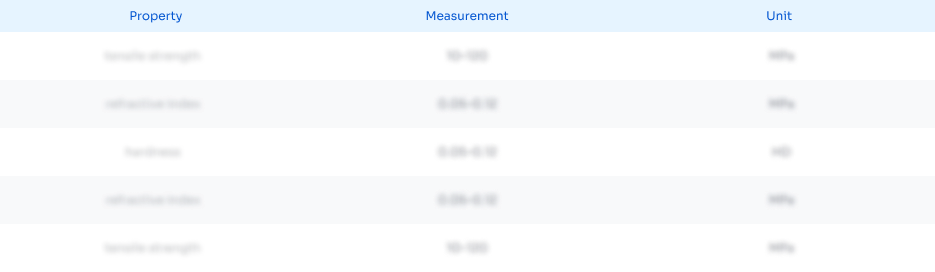
Abstract
Description
Claims
Application Information

- R&D
- Intellectual Property
- Life Sciences
- Materials
- Tech Scout
- Unparalleled Data Quality
- Higher Quality Content
- 60% Fewer Hallucinations
Browse by: Latest US Patents, China's latest patents, Technical Efficacy Thesaurus, Application Domain, Technology Topic, Popular Technical Reports.
© 2025 PatSnap. All rights reserved.Legal|Privacy policy|Modern Slavery Act Transparency Statement|Sitemap|About US| Contact US: help@patsnap.com