Method and device for degassing solid polymer and recovering effluent gas
A solid polymer and exhaust gas technology, which is applied in the field of solvents and unreacted monomers in polyolefin resins, can solve the problems of low degassing efficiency and exhaust gas recovery efficiency, ineffective separation of hydrogen, and increased safety hazards. , to achieve significant economic benefits and environmental friendliness, strong practical significance and application value, and reduce system energy consumption
- Summary
- Abstract
- Description
- Claims
- Application Information
AI Technical Summary
Problems solved by technology
Method used
Image
Examples
Embodiment 1
[0047] like figure 2 As shown, a solid polymer degassing and exhaust gas recovery device includes a degassing container 4, a gas separation device and a recovery device.
[0048] The degassing container is a cylindrical structure, and two gas collection devices for separating the degassing area and collecting exhaust gas are arranged inside. The first gas collection device 61 is arranged in the middle of the degassing container 1, and the second gas collection device 61 The collection device 62 is arranged at the bottom of the degassing container 4 near the outlet, the top of the degassing container 4 is a primary degassing zone, the middle part of the degassing container 4 and the area where the second gas collecting device 62 is located is a secondary degassing zone, The lower part of the degassing container 4 below the second gas collection device 61 is a three-stage degassing zone.
[0049]The recovery device includes a first compressor 51 , a cooler 6 , a condenser 7 an...
Embodiment 2
[0055] The same device as in Example 1 was used to produce ethylene-hexene copolymerized linear low-density polyethylene (LLDPE) products by a gas-phase fluidized bed process, with a reaction temperature of 88° C. and a reaction pressure of 2.1 MPa, using non-condensing operation. The LLDPE product discharged from the reactor enters the top of the degassing vessel 4 driven by the conveying gas, and the flow rate of each component in the feed stream 40 is: LLDPE powder 40t / h, nitrogen 180kg / h, hydrogen 3kg / h, ethylene 2600kg / h, hexene 2000kg / h. Among them, ethylene and hexene are unreacted monomers without solvent. The temperature of the degassing container 4 is 81° C., the pressure is 20 kPa, the first degassing medium is ethylene, and the flow rate of the first degassing medium stream 10 is 400 kg / h. The first exhaust gas 11 is compressed and condensed, the outlet pressure of the first compressor 51 is 2.0 MPa, and the outlet temperature of the cooler 6 is 30°C. After more ...
Embodiment 3
[0060] like image 3 As shown, a solid polymer degassing and exhaust gas recovery device includes a degassing container 4, a gas separation device and a recovery device.
[0061] Shown degassing container and gas separation device are identical with the device in embodiment 1 and 2, and described recovery device is in figure 2 On the basis of the shown device, a non-porous composite membrane primary separation device 92 is added between the condenser 7 and the porous membrane separation device 8 .
[0062] The ethylene-butene copolymerized linear low density polyethylene (LLDPE) product is produced by the gas phase fluidized bed process, the reaction temperature is 88°C, the reaction pressure is 2.1MPa, and the condensation operation is adopted. The LLDPE product discharged from the reactor enters the top of the degassing vessel 4 driven by the transport gas, and the flow rate of each component in the feed stream 40 is: LLDPE powder 40t / h, nitrogen 160kg / h, hydrogen 3kg / h, e...
PUM
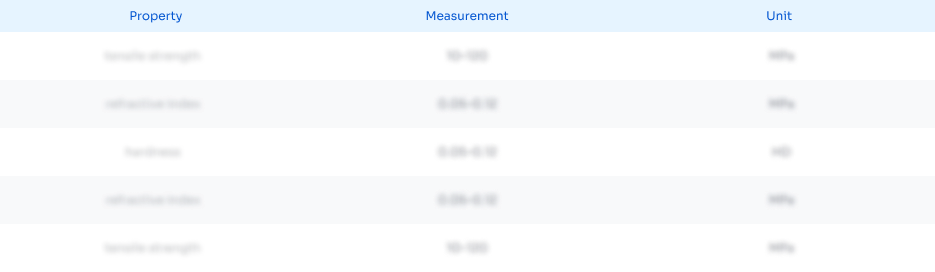
Abstract
Description
Claims
Application Information

- Generate Ideas
- Intellectual Property
- Life Sciences
- Materials
- Tech Scout
- Unparalleled Data Quality
- Higher Quality Content
- 60% Fewer Hallucinations
Browse by: Latest US Patents, China's latest patents, Technical Efficacy Thesaurus, Application Domain, Technology Topic, Popular Technical Reports.
© 2025 PatSnap. All rights reserved.Legal|Privacy policy|Modern Slavery Act Transparency Statement|Sitemap|About US| Contact US: help@patsnap.com