Preparation method of 2,3-dichloropyridine
A technology of dichloropyridine and trichloropyridine, which is applied in the field of important fine chemical intermediates 2, can solve the problems of multiple synthesis steps, complex reaction types, and high raw material prices, and achieve high-efficiency separation and recovery technology, novel and simple process routes
- Summary
- Abstract
- Description
- Claims
- Application Information
AI Technical Summary
Problems solved by technology
Method used
Image
Examples
Embodiment 1
[0033] Chlorination reaction
[0034] Weigh 1480.0 g of 2,6-dichloropyridine and anhydrous FeCl 3 Mix 89.2g in a 2000ml four-neck flask and heat up. When the temperature reaches 100-120°C, introduce chlorine gas. After the reaction is complete, cool down to 100°C, rectify under reduced pressure, at -0.1MPa, top temperature 118-124°C The product fraction is collected next, and the low-concentration distillate produced during the rectification process can also be applied to the next batch of re-reaction or to the next batch of re-distillation and purification. After mechanical application, 1715.0 g of 2,3,6-trichloropyridine was finally obtained, with a total yield of 94.0% and a purity of ≥99.5%.
[0035] hydrogenation reaction
[0036] Put 557.8g of 2,3,6-trichloropyridine, 123.5g of triethylamine, 8.4g of palladium carbon, and 1673g of toluene prepared in the chlorination reaction into the reactor at one time, raise the temperature to 60-80°C, and feed Hydrogen is carried ...
Embodiment 2
[0040] Chlorination reaction
[0041] Take by weighing 2,6-dichloropyridine 299.2g and reclaimed distillate liquid 533.7g (wherein 2,6-dichloropyridine accounts for 86.1%, 2,3,6-trichloropyridine accounts for 9%), and anhydrous AlCl 3 Put 36.5g in a 1000ml four-necked flask and mix it. When the temperature rises to 120-140°C, chlorine gas is introduced. After the reaction is complete, cool down to 100°C, rectify under reduced pressure, and collect at -0.1MPa at a top temperature of 118-124°C. Product fractions, low-concentration products that are evaporated can be applied mechanically to the next batch of re-reaction or to the next batch of rectification and purification; after the mechanical application, 890.7g of 2,3,6-trichloropyridine is finally obtained, and the total yield after the mechanical application is 95.2% , purity ≥ 99.5%.
[0042] hydrogenation reaction
[0043] 1340 g of the toluene solution of 2,3,6-trichloropyridine recovered in Example 1 can be added with 4...
PUM
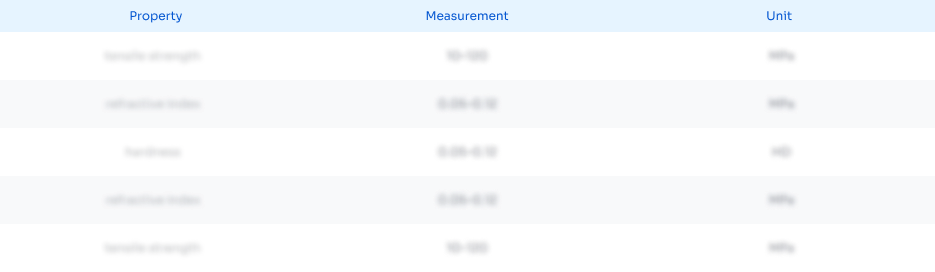
Abstract
Description
Claims
Application Information

- R&D
- Intellectual Property
- Life Sciences
- Materials
- Tech Scout
- Unparalleled Data Quality
- Higher Quality Content
- 60% Fewer Hallucinations
Browse by: Latest US Patents, China's latest patents, Technical Efficacy Thesaurus, Application Domain, Technology Topic, Popular Technical Reports.
© 2025 PatSnap. All rights reserved.Legal|Privacy policy|Modern Slavery Act Transparency Statement|Sitemap|About US| Contact US: help@patsnap.com