Method for two-stage coal gasification on composite external heat fixed bed and gas furnace
A two-stage, coal gasification technology, which is applied in the field of gas furnace and composite external heat fixed bed two-stage coal gasification, can solve the problems of low carbonization efficiency, high steam decomposition rate, and difficult treatment of phenol water.
- Summary
- Abstract
- Description
- Claims
- Application Information
AI Technical Summary
Problems solved by technology
Method used
Image
Examples
Embodiment 1
[0114] Such as figure 1 As shown, the flow chart of the two-stage coal gasification method of continuous gas production combined with external heat fixed bed, the non-anthracite raw material for gas production is controlled by the gas lock coal feeding device 1 and enters the fixed bed coal gasification retort section 2, and the raw material coal in the retort section is externally Thermal dry distillation becomes semi-coke, and the final temperature of dry distillation is below 900°C. The hot semi-coke then enters the gasification section 3. In the gasification section 3, it is continuously gasified with the oxidant and gasification agent introduced from the bottom, and the gasification section 3 is gasified to produce After the coal gas leaves the gasification section, it exchanges heat indirectly with the raw coal in the carbonization section 2 to provide carbonization heat. The insufficient heat is supplied to the raw coal in the carbonization section 2 by indirect heat exc...
Embodiment 2
[0118] Such as figure 1 As shown, the process flow diagram of continuous gas production compound external heating fixed bed two-stage coal gasification method.
[0119] In this embodiment, oxygen is used as an oxidant, and steam is used as a gasification agent to continuously pass through the gasification section to obtain feed gas for the production of synthetic ammonia, methanol, methane, and hydrogen, and the rest are the same as in Embodiment 1.
Embodiment 3
[0121] Such as figure 1 As shown, the process flow diagram of continuous gas production compound external heating fixed bed two-stage coal gasification method.
[0122] In this embodiment, oxygen is used as an oxidant, and carbon dioxide is used as a gasification agent to continuously pass through the gasification section to prepare a raw material gas rich in carbon monoxide. The feed gas rich in carbon monoxide can be used to produce chemical products such as acetic acid, formic acid, and sodium formate, and the rest are the same as in Embodiment 1.
PUM
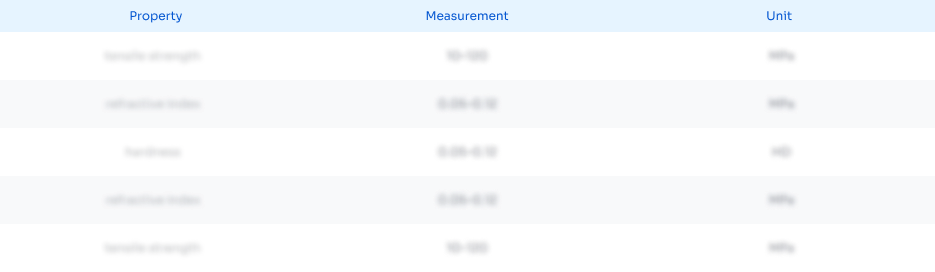
Abstract
Description
Claims
Application Information

- R&D
- Intellectual Property
- Life Sciences
- Materials
- Tech Scout
- Unparalleled Data Quality
- Higher Quality Content
- 60% Fewer Hallucinations
Browse by: Latest US Patents, China's latest patents, Technical Efficacy Thesaurus, Application Domain, Technology Topic, Popular Technical Reports.
© 2025 PatSnap. All rights reserved.Legal|Privacy policy|Modern Slavery Act Transparency Statement|Sitemap|About US| Contact US: help@patsnap.com