Method for preparing high-grade synthetic rutile
An artificial rutile, high-grade technology, applied in the direction of titanium dioxide, titanium oxide/hydroxide, etc., can solve the problems of low quality of titanium-rich material, increase investment cost, improve technical operation difficulty, etc., achieve low equipment investment, low cost, The effect of broad applicability
- Summary
- Abstract
- Description
- Claims
- Application Information
AI Technical Summary
Problems solved by technology
Method used
Image
Examples
Embodiment 1
[0023] 20% sodium hydroxide solution and 75% electric furnace titanium slag with a particle size of <0.1 mm were mixed according to the weight-liquid-solid ratio of 8:1, and reacted at a temperature of 80°C for 10 hours. At this time, the pressure of the system was the standard atmospheric pressure of 0.1MPa. After the reaction, after operations such as filtration and washing, the alkali leaching residue is obtained. The alkali leaching slag is pre-oxidized in the electric furnace, the pre-oxidation temperature is 700 ℃, the pre-oxidation time is 4h, and the air flow rate is 1000 L / h. The titanium slag after the pre-oxidation treatment was mixed with the modifying agent ammonium hydrogen phosphate in a weight ratio of 5:1, and modified at 800°C for 3 hours to obtain the modified slag. 20% sulfuric acid solution and modified slag were mixed according to the weight-liquid-solid ratio of 7:1, the reaction temperature was kept at 130°C, the reaction pressure was 0.5MPa, and the ac...
Embodiment 2
[0026] The mixture of 30% potassium hydroxide solution and 10% lithium hydroxide solution is mixed with 75% electric furnace titanium slag with a particle size of <0.1 mm according to the weight-liquid-solid ratio of 4:1, and reacted at a temperature of 130°C for 1 hour. The pressure is 1.0 MPa. After the reaction, after operations such as filtration and washing, the alkali leaching residue is obtained. The alkali leaching slag is pre-oxidized in the electric furnace, the pre-oxidation temperature is 1000 ℃, the pre-oxidation time is 1h, and the air flow rate is 950 L / h. The titanium slag after the pre-oxidation treatment was mixed with the modifying agent ammonium polyhydrogen phosphate according to the weight ratio of 3:1, and modified at 600°C for 7 hours to obtain the modified slag. The mixture of 15% hydrochloric acid solution and 30% nitric acid solution is mixed with the modified slag according to the weight liquid-solid ratio of 5: 1, the reaction temperature is kept ...
Embodiment 3
[0029] Ammonia water and 75% electric furnace titanium slag with a particle size <0.1 mm were mixed according to the weight-liquid-solid ratio of 7:1, and reacted at a temperature of 95°C for 6 hours. At this time, the pressure of the system was the standard atmospheric pressure of 0.1MPa. After the reaction, after operations such as filtration and washing, the alkali leaching residue is obtained. The alkali leaching slag is pre-oxidized in the electric furnace, the pre-oxidation temperature is 800 ℃, the pre-oxidation time is 3h, and the air flow rate is 840 L / h. The pre-oxidized titanium slag was mixed with the modifier phosphorus pentoxide in a weight ratio of 1:1, and modified at 700° C. for 6 hours to obtain the modified slag. 40% nitric acid solution and modified slag were mixed according to the weight-liquid-solid ratio of 15:1, the reaction temperature was kept at 100°C, the reaction pressure was 0.1MPa, and the acid leaching time was 10h. The reacted acid leaching re...
PUM
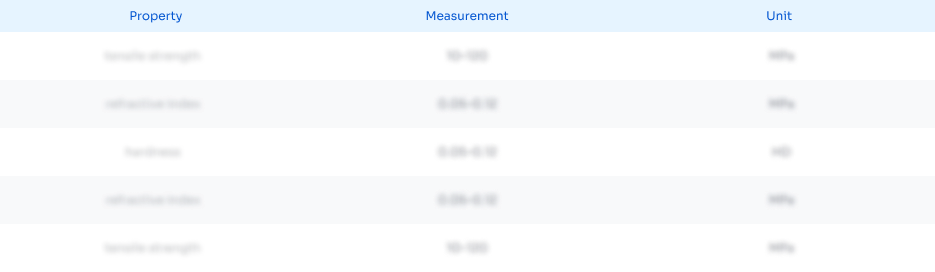
Abstract
Description
Claims
Application Information

- Generate Ideas
- Intellectual Property
- Life Sciences
- Materials
- Tech Scout
- Unparalleled Data Quality
- Higher Quality Content
- 60% Fewer Hallucinations
Browse by: Latest US Patents, China's latest patents, Technical Efficacy Thesaurus, Application Domain, Technology Topic, Popular Technical Reports.
© 2025 PatSnap. All rights reserved.Legal|Privacy policy|Modern Slavery Act Transparency Statement|Sitemap|About US| Contact US: help@patsnap.com