Method for implementing semi-dry plating on surface of plastic substrate
A base material surface, semi-dry method, applied in the direction of sputtering coating, superimposed layer coating, vacuum evaporation coating, etc., can solve the problems of sewage discharge, environmental pollution, environmental pollution, etc., to expand the scope and reduce Pollution, the effect of simplifying the electroplating process
- Summary
- Abstract
- Description
- Claims
- Application Information
AI Technical Summary
Problems solved by technology
Method used
Image
Examples
Embodiment 1
[0025] The semi-dry electroplating technological process of embodiment 1 plastic part surface smooth situation
[0026] The specific steps of semi-dry electroplating on the surface of the car door handle of PC+ABS plastic substrate are as follows:
[0027] Step 1 (injection molding): Dry the PC+ABS engineering plastic resin at 80°C for 4 hours, and then mold it into the plastic part of the car door handle by injection molding, and the surface of the plastic part is smooth.
[0028] Step 2 (plastic parts cleaning and plasma surface modification): the cleaning (dry cleaning) process before coating is to wipe the surface with anhydrous alcohol, and plasma glow cleaning in the PVD furnace. The plasma glow cleaning parameters are: Ar flow rate 65sccm, glow cleaning time 5min, bias voltage 70V, bias vacuum ratio 70%, ion source current 0.3A.
[0029] The plastic parts after cleaning are put into the vacuum furnace to carry out plasma surface modification, and the parameter of plasm...
Embodiment 2
[0033] The semi-dry electroplating technological process of the rough and uneven situation of the rubber part surface of embodiment 2
[0034] The specific steps for semi-dry electroplating on the surface of the plastic substrate of the faucet handle of polyamide modified engineering plastics are as follows:
[0035] Step 1 (injection molding): Dry the polyamide modified rubber particles at 120°C for 4 hours, and then mold them into plastic parts for faucet handles by injection molding. Since glass fiber is used in the modified formula, there are tiny oranges on the surface of the injected plastic parts. skin texture.
[0036] Step 2 (plastic parts cleaning and plasma surface modification): the cleaning (dry cleaning) process before coating is anhydrous alcohol wiping, and plasma glow cleaning in the PVD furnace. The plasma glow cleaning parameters are: Ar gas flow 65sccm, glow cleaning time 5min, ion source current 0.3A, bias voltage 70V, bias voltage vacuum ratio 70%, ion s...
Embodiment 3
[0042] Implementation of semi-dry electroplating technology on the surface of large-density ball head plastic substrate of polyamide modified engineering plastics
[0043] Step 1 (injection molding): Dry the polyamide-modified rubber particles at 120°C for 4 hours, and then mold them into rubber parts with high-density ball heads by injection molding, and the surface of the rubber parts is smooth.
[0044] Step 2 (cleaning and surface modification of plastic parts): Put the dried plastic parts into a vacuum furnace for plasma glow cleaning and plasma surface modification. The parameters of plasma glow cleaning are: Ar gas flow rate 65sccm, glow cleaning Time 5min, ion source current 0.3A, bias voltage 70V, bias voltage vacuum ratio 70%, ion source current 0.3A plasma glow surface modification parameters are: O 2 The gas flow is 100 sccm, the glow surface modification time is 10 minutes, the bias voltage is 70V, and the bias vacuum ratio is 70%.
[0045] Step 3 (PVD metal bott...
PUM
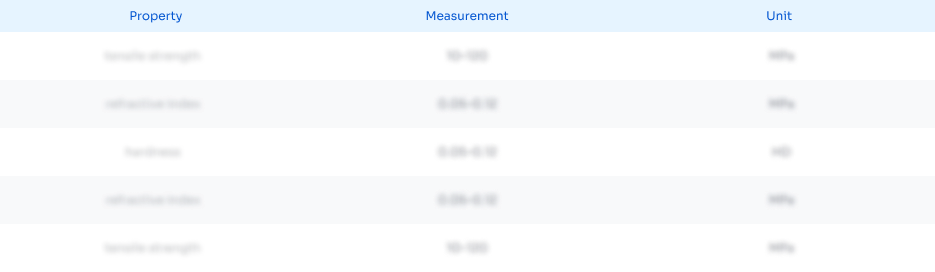
Abstract
Description
Claims
Application Information

- R&D
- Intellectual Property
- Life Sciences
- Materials
- Tech Scout
- Unparalleled Data Quality
- Higher Quality Content
- 60% Fewer Hallucinations
Browse by: Latest US Patents, China's latest patents, Technical Efficacy Thesaurus, Application Domain, Technology Topic, Popular Technical Reports.
© 2025 PatSnap. All rights reserved.Legal|Privacy policy|Modern Slavery Act Transparency Statement|Sitemap|About US| Contact US: help@patsnap.com