Control method for vanadium extraction by converter for removing vanadium and holding carbon
A control method and vanadium removal technology, which is applied in the field of metallurgical vanadium extraction, can solve the problems of shortening the optimal temperature range of vanadium oxidation, high Mfe in slag, and many factors at the end point composition and temperature, so as to eliminate the end point blowing phenomenon and recover The effect of increasing the rate and improving the main technical indicators
- Summary
- Abstract
- Description
- Claims
- Application Information
AI Technical Summary
Problems solved by technology
Method used
Image
Examples
Embodiment 1
[0033] This furnace is a non-slagging furnace. The vanadium extraction converter is charged with 115 tons of molten iron, molten iron [C] 4.37%, [Si+Ti] 0.47% [V] 0.238%, the temperature is 1268 ° C, 7 tons of iron nuggets are added, and the output The amount of semi-steel is 116 tons, the target semi-steel [C] 3.85%, [V] ≤ 0.04%, and the temperature is 1380-1390°C. After the start of blowing, the temperature of the molten pool rises slowly, and the carbon-oxygen reaction gradually becomes more intense. At 35% of the planned oxygen step (the plan is the percentage of oxygen supply), the CO% is 5%. After adding iron oxide balls according to 3kg / t semi-steel, the CO% decreases due to the decrease in the temperature of the molten pool to inhibit the carbon-oxygen reaction. With the gradual progress of the blowing process, the temperature gradually rises. When the blowing progresses to the planned oxygen step of 67%, the CO% is 5%. After adding iron oxide balls according to 3kg / t...
Embodiment 2
[0036]This furnace is a non-slagging furnace. The vanadium extraction converter is charged with 114 tons of molten iron, molten iron [C] 4.41%, [Si+Ti] 0.65%, [V] 0.306%, the temperature is 1301 ° C, and 8 tons of iron nuggets are added. The amount of semi-steel produced is 116 tons, the target semi-steel [C] 3.80-3.90%, [V]≤0.04%, and the temperature is 1380-1390°C. After the start of blowing, the temperature of the molten pool rises slowly, and the carbon-oxygen reaction gradually becomes more intense. At 39% of the planned oxygen step (the plan is the percentage of oxygen supply), the CO% is 5%. After adding iron oxide balls according to 5kg / t semi-steel, the CO% decreases due to the decrease in the temperature of the molten pool to inhibit the carbon-oxygen reaction. With the gradual progress of the blowing process, the temperature gradually rises. When the blowing progresses to the planned oxygen step of 75%, the CO% is 5%, adding iron oxide balls according to 5kg / t semi...
Embodiment 3
[0039] This furnace is a slag dumping furnace. The vanadium extraction converter is charged with 115 tons of molten iron, molten iron [C] 4.37%, [Si+Ti] 0.42%, [V] 0.296%, the temperature is 1296°C, and 5 tons of iron nuggets are added. The amount of semi-steel is 114 tons, the target semi-steel [C] 3.75-3.85%, [V] ≤ 0.05%, and the temperature is 1395-1405°C. After the start of blowing, the temperature of the molten pool rises slowly, and the carbon-oxygen reaction gradually becomes more intense. At 24% of the planned oxygen step (the plan is the percentage of oxygen supply), the CO% is 5%. After adding iron oxide balls according to the 3.5kg / t semi-steel, the carbon-oxygen reaction is inhibited by the drop in the molten pool temperature, and the CO% drops . With the gradual progress of the blowing process, the temperature gradually rises. When the blowing progresses to the planned oxygen step of 43%, the CO% is 5%, adding iron oxide balls according to 3kg / t semi-steel, and ...
PUM
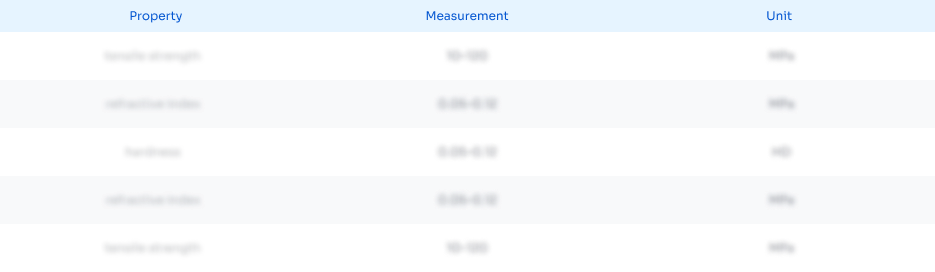
Abstract
Description
Claims
Application Information

- Generate Ideas
- Intellectual Property
- Life Sciences
- Materials
- Tech Scout
- Unparalleled Data Quality
- Higher Quality Content
- 60% Fewer Hallucinations
Browse by: Latest US Patents, China's latest patents, Technical Efficacy Thesaurus, Application Domain, Technology Topic, Popular Technical Reports.
© 2025 PatSnap. All rights reserved.Legal|Privacy policy|Modern Slavery Act Transparency Statement|Sitemap|About US| Contact US: help@patsnap.com