Polycarbonate resin composition and molded body of the same
A technology of polycarbonate resin and composition, applied in the field of polycarbonate resin composition and its molded body, can solve the problems of small elongation, no effect of modifier, insufficient reaction of acid anhydride modified PO, and the like, Achieve low gloss, excellent fluidity and chemical resistance, excellent impact resistance and flexural strength
- Summary
- Abstract
- Description
- Claims
- Application Information
AI Technical Summary
Problems solved by technology
Method used
Image
Examples
Embodiment 1~5 and comparative example 1~7
[0096] After dry mixing the ingredients according to the mixing ratios shown in Table 1 and Table 2, use a twin-shaft mixer (TEX44, manufactured by Japan Steel Works) at a set temperature of 250°C to prolong the stagnation time and increase the number of mixing blocks. Melt-kneading was carried out while discharging the amount to obtain pellets.
[0097] After drying the obtained pellets at 120°C for 6 hours or more, test pieces were prepared by injection molding (injection molding temperature 270°C, mold temperature 80°C), and physical properties were evaluated according to the following methods. The results are shown in Table 1 and Table 2.
[0098]
[0099] (1) Tensile strength, tensile modulus of elasticity, tensile elongation (test piece thickness 3.0mm)
[0100] According to JIS K 7162
[0101] (2) Izod impact strength (with notch) (test piece thickness 3.0mm)
[0102] According to JIS K 7110
[0103] (3) High-speed drop weight impact test (test piece 70×70×3mm fla...
Embodiment 6 and 7
[0122] To the compositions of Examples 1 and 2, 3000 ppm of carbon black (manufactured by Mitsubishi Chemical Corporation) was further added for black coloring, and the same pellets as in Example 1 were obtained. Using the pellets, a corrugated flat plate of 140 x 140 x 2 mm was molded by injection molding and used as a test piece. Using a scratch tester (Scratch Tester) manufactured by Kato-Tec, a scratch test was performed under the conditions of a surface load of 30 N and a bead printing speed of 100 mm / sec on the test piece, and the evaluation of scratch whitening property was performed visually. In addition, its color tone was evaluated by visual inspection. The evaluation results are shown in Table 3.
PUM
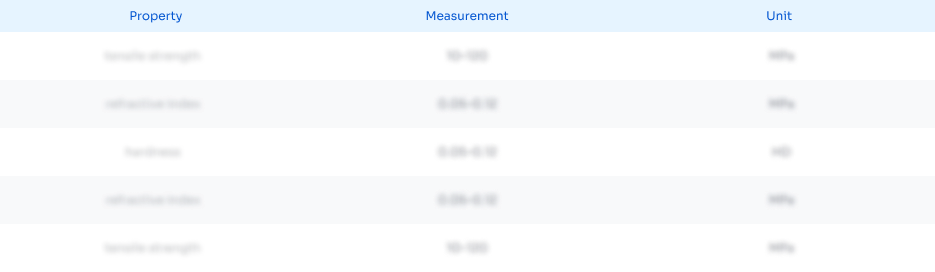
Abstract
Description
Claims
Application Information

- R&D
- Intellectual Property
- Life Sciences
- Materials
- Tech Scout
- Unparalleled Data Quality
- Higher Quality Content
- 60% Fewer Hallucinations
Browse by: Latest US Patents, China's latest patents, Technical Efficacy Thesaurus, Application Domain, Technology Topic, Popular Technical Reports.
© 2025 PatSnap. All rights reserved.Legal|Privacy policy|Modern Slavery Act Transparency Statement|Sitemap|About US| Contact US: help@patsnap.com