Injection mould provided wtih core-pulling mechanism driven by mould opening and closing actions
A technology of injection mold and core-pulling mechanism, which is applied in the field of improvement of the core-pulling mechanism in the mould, can solve problems such as core-pulling, and achieve the effects of saving processing costs, smooth action, and synchronous action
- Summary
- Abstract
- Description
- Claims
- Application Information
AI Technical Summary
Problems solved by technology
Method used
Image
Examples
Embodiment 1
[0048] see figure 1 , the cylinder a is placed in the movable template b, one end of the passive slider e is the forming glue position g, and the other end is opened with a "T"-shaped groove, and the active slider d is fixed with a piston rod h that is fixed to the direction of movement of the piston rod h of the cylinder a. The "T" shaped block with an oblique angle, the "T" shaped block on the active slider d is slidingly matched with the "T" shaped groove on the passive slider e. At the same time, there is a "T"-shaped groove at the bottom of the active slider d, which is matched with the joint of the piston rod h of the oil cylinder a. During the core-pulling process, the oil cylinder a pulls the active slider d to move along the direction of the piston rod h, thereby driving The passive slider e moves toward the interior of the product c in a direction perpendicular to the moving direction of the piston rod h in the insert groove, so as to realize core pulling and forming...
Embodiment 2
[0057] Different from the above-mentioned embodiments, the inclined slide between the active slider 2-1 and the passive slider 2-2 is slidably fitted into an inverted "L"-shaped block 2-10 and an oblique inverted "L"-shaped groove 2-11 The sliding fit, the inverted "L" shaped block 2-10 is inserted into the inclined inverted "L" shaped groove 2-11, that is, as Figure 7-1 and Figure 7-2 The shown "draw hook" structure ramp is matched.
PUM
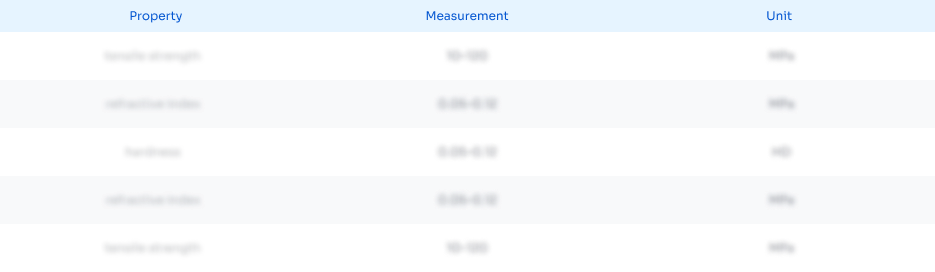
Abstract
Description
Claims
Application Information

- R&D Engineer
- R&D Manager
- IP Professional
- Industry Leading Data Capabilities
- Powerful AI technology
- Patent DNA Extraction
Browse by: Latest US Patents, China's latest patents, Technical Efficacy Thesaurus, Application Domain, Technology Topic, Popular Technical Reports.
© 2024 PatSnap. All rights reserved.Legal|Privacy policy|Modern Slavery Act Transparency Statement|Sitemap|About US| Contact US: help@patsnap.com