Low smoke non-halogen one-stage process silane naturally crosslinked polyolefin cable material and preparation method thereof
A polyolefin cable material, natural cross-linking technology, applied in the direction of insulated cables, cables, circuits, etc., can solve the problems of low temperature resistance level of wires and cables, large damage to materials, reduced electrical properties of materials, etc., and achieve reliable extrusion performance. and cross-linking degree, improve physical properties, and reduce the effect of smoke generation
- Summary
- Abstract
- Description
- Claims
- Application Information
AI Technical Summary
Problems solved by technology
Method used
Examples
Embodiment 1
[0036] Example 1: A low-smoke and halogen-free one-step silane naturally crosslinked polyolefin cable material and its preparation method
[0037] 1. Preparation of modified flame retardant:
[0038] Weigh 70 parts of magnesium hydroxide H-5 (Yabao), 70 parts of aluminum hydroxide OL-104LE (Yabao), and 5 parts of γ-aminopropyltriethoxysilane (KH-550) by weight, and weigh After measuring, add the flame retardant into the closed mixer, spray KH-550 to modify the surface of the flame retardant, and mix it at a high speed for 30 minutes at a temperature of 80°C, then release it. The obtained modified flame retardant agent.
[0039] 2. Preparation of flame retardant masterbatch:
[0040] Weigh 40 parts of linear low density polyethylene (DFDA 7042), 30 parts of polyethylene octene co-elastomer (Exxon 0230), 30 parts of ethylene-vinyl acetate copolymer (DuPont 265), modified flame retardant Mix 140 parts of the agent in a closed high-speed mixer, and then use an internal mixer to...
Embodiment 2 4
[0045] Embodiments 2-4: A low-smoke and halogen-free one-step silane naturally crosslinked polyolefin cable material and its preparation method
[0046] 1. The formula of flame retardant masterbatch is as follows:
[0047] LLDPE POE EVA Aluminum hydroxide magnesium hydroxide Zinc borate Embodiment two 50 copies 20 copies 30 copies 60 copies 100 copies Embodiment three 20 copies 40 copies 40 copies 70 copies 60 copies Embodiment Four 35 copies 30 copies 30 copies 70 copies 75 copies
[0048] 2. The formula of the catalyst masterbatch is as follows:
[0049] LDPE catalyst antioxidant metal deactivator lubricant Embodiment two 100 copies 5 copies 3 copies 6 servings 13 copies Embodiment three 100 copies 20 copies 20 copies 7 copies 17 copies Embodiment Four 100 copies 10 copies 5 copies 6 servings 30 copies
[0050] Note: 1. Exampl...
PUM
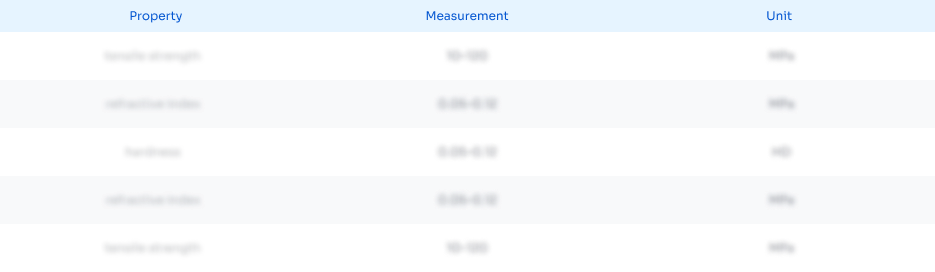
Abstract
Description
Claims
Application Information

- Generate Ideas
- Intellectual Property
- Life Sciences
- Materials
- Tech Scout
- Unparalleled Data Quality
- Higher Quality Content
- 60% Fewer Hallucinations
Browse by: Latest US Patents, China's latest patents, Technical Efficacy Thesaurus, Application Domain, Technology Topic, Popular Technical Reports.
© 2025 PatSnap. All rights reserved.Legal|Privacy policy|Modern Slavery Act Transparency Statement|Sitemap|About US| Contact US: help@patsnap.com