Method for preparing porous ceramsite filter material from slate saw mud
A technology for porous pottery and slate, applied in separation methods, chemical instruments and methods, filtration and separation, etc., can solve the problems of difficult utilization, poor plasticity, uneven particle size and thickness, and achieve uniform porosity and low wear rate. , The effect of low production cost
- Summary
- Abstract
- Description
- Claims
- Application Information
AI Technical Summary
Problems solved by technology
Method used
Image
Examples
Embodiment 1
[0017] The chemical composition of the used slate saw mud (dried) is shown in Table 2.
[0018] The chemical composition (%) of table 2 slate saw mud
[0019] SiO2
Al2O3
CaO
MgO
K2O+NaO
Fe2O3
FeO
57.30
18.90
0.65
0.60
3.85
0.80
7.50
SO2
C
MnO
P2O5
LOSS
0.20
2.80
0.15
0.95
6.30
[0020] The ratio of raw materials is (mass percentage): 60% of slate saw mud (dry base), 30% of slate dry powder, and 10% of diatomite.
[0021] Preparation Process:
[0022] (1) Spray slate saw mud, dry slate powder and diatomaceous earth into a twin-shaft mixer to make cue balls of φ1-1.5mm;
[0023] (2) The cue ball is rolled into a spherical particle of φ3-8mm in the sprayed water in the granulator;
[0024] (3) The pellets are fed into the pre-calcination section of the rotary kiln and pre-fired at 200-500°C for 10 minutes, and then enter...
Embodiment 2
[0030] The ratio of raw materials is: slate saw mud (dry base) 70%, slate dry powder 25%, diatomaceous earth 5%.
[0031] Technological process is the same with embodiment 1.
Embodiment 3
[0033] The ratio of raw materials is: slate saw mud (dry base) 65%, slate dry powder 28%, diatomite 7%.
[0034] Technological process is the same with embodiment 1.
[0035] Some performance technical indicators of the products of Examples 2-3 are shown in Table 3.
[0036] Table 3 Some performance indicators of different example products
[0037]
[0038] *Take 10 φ8mm±1mm material balls to measure the compressive strength on the electronic universal testing machine, and take the average value.
PUM
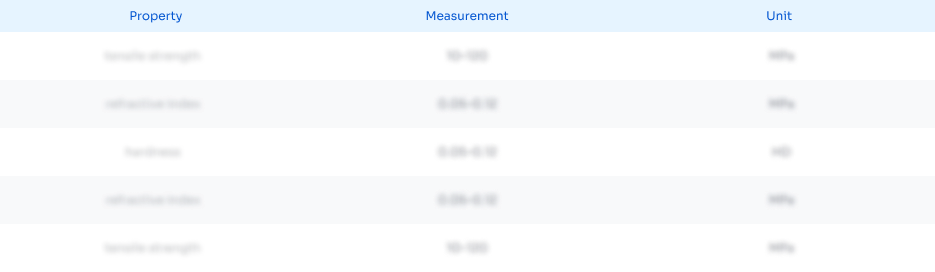
Abstract
Description
Claims
Application Information

- R&D
- Intellectual Property
- Life Sciences
- Materials
- Tech Scout
- Unparalleled Data Quality
- Higher Quality Content
- 60% Fewer Hallucinations
Browse by: Latest US Patents, China's latest patents, Technical Efficacy Thesaurus, Application Domain, Technology Topic, Popular Technical Reports.
© 2025 PatSnap. All rights reserved.Legal|Privacy policy|Modern Slavery Act Transparency Statement|Sitemap|About US| Contact US: help@patsnap.com