Method for preparing wood plastic composite material sections with embossing
A wood-plastic composite material and profile technology, which is applied in the field of profile processing technology, can solve the problems of negative impact on the mechanical properties of profiles, damage to crusting, waste of labor, etc. Effect
- Summary
- Abstract
- Description
- Claims
- Application Information
AI Technical Summary
Problems solved by technology
Method used
Image
Examples
Embodiment 1
[0024] The processing equipment used in the original preparation of wood-plastic composite profiles is as follows: figure 1 As shown, it mainly includes a dryer 2, an extruder 3, a cooling and setting table 4, a tractor 5 and a cutting device 6, and the feed port of the dryer 2 is provided with a feeding cylinder 1 for feeding, and the drying The discharge port of the extruder 2 is connected with the feed port of the extruder 3. The cooling and shaping table 4 is provided with a calibrating die 41 and a cooling water tank 42. The calibrating die 41 is close to the head of the extruder 3. If necessary, use figure 1 If the profile prepared by the processing equipment shown is embossed, the embossing machine needs to be used for secondary processing. For this reason, the present invention proposes a kind of preparation method of wood-plastic composite profile, and the processing equipment that it adopts is as figure 2 as shown, figure 2 The processing equipment shown is in f...
Embodiment 2
[0041] The preparation process of this embodiment is basically the same as that of Example 1, the only difference is that the color masterbatch is added in step ②, and the granular material and the color masterbatch are firstly mixed according to actual requirements; then the prepared particles Granular materials and color masterbatch are put into the dryer 2 through the upper barrel 1, and the prepared granular materials and color masterbatch are dried, and the drying temperature does not exceed 85°C. The profiles made by adding color masterbatch are not only rich in color, but also do not need to be painted. Here, the color masterbatch directly adopts the commercially available color masterbatch.
PUM
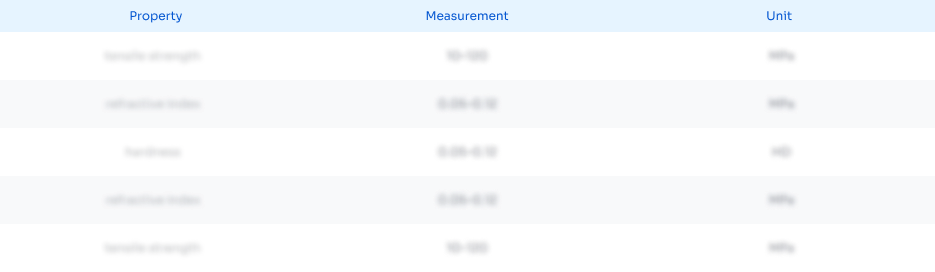
Abstract
Description
Claims
Application Information

- R&D
- Intellectual Property
- Life Sciences
- Materials
- Tech Scout
- Unparalleled Data Quality
- Higher Quality Content
- 60% Fewer Hallucinations
Browse by: Latest US Patents, China's latest patents, Technical Efficacy Thesaurus, Application Domain, Technology Topic, Popular Technical Reports.
© 2025 PatSnap. All rights reserved.Legal|Privacy policy|Modern Slavery Act Transparency Statement|Sitemap|About US| Contact US: help@patsnap.com