Method for recycling metal from waste catalyst containing molybdenum and nickel
A waste catalyst and metal technology, applied in the field of nickel, recycling molybdenum-containing and aluminum compounds, can solve the problems of low recovery rate, high processing cost, low nickel purity, etc., and achieves simple process, low energy consumption, and complete reaction. Effect
- Summary
- Abstract
- Description
- Claims
- Application Information
AI Technical Summary
Problems solved by technology
Method used
Examples
Embodiment 1
[0033] 100 g of 3996 waste hydrogenation catalyst (3996 is a heavy distillate oil hydrocracking pretreatment catalyst developed and produced by Fushun Petrochemical Research Institute) was roasted at 350° C. for 3 hours, and then crushed to 120 mesh after cooling. 88.4 g was obtained, and the contents of molybdenum and nickel (by weight of oxide) were analyzed to be 22.9% and 3.1%, respectively. Mix with alkaline matter, the weight ratio of sodium carbonate and spent catalyst is 1:1 (weight is about 88g), the weight ratio of sodium bicarbonate and spent catalyst is 0.5:1 (weight is about 44g), the weight ratio of sodium hydroxide and spent catalyst is The weight ratio is 0.1:1 (the weight is about 9g). The powder after mixing was pulverized and calcined at 650° C. for 10 hours, and the weight of the powder after cooling was 213.6 g. The volume of the mixed acid solution prepared is 2100mL, wherein the concentration of sulfuric acid is 10%, the concentration of nitric acid is ...
Embodiment 2
[0035]100 g of the 3996 waste hydrogenation catalyst was calcined at 500° C. for 3 hours, and then pulverized to 120 mesh after cooling. Obtained 79.6g, the content of molybdenum and nickel (based on oxide weight) was analyzed to be 23.7% and 3.6%, respectively. Mix with alkaline matter, the weight ratio of sodium carbonate and spent catalyst is 2:1 (weight is about 160g), the weight ratio of sodium bicarbonate and spent catalyst is 0.2:1 (weight is about 16g), the weight ratio of sodium hydroxide and spent catalyst is The weight ratio is 0.2:1 (the weight is about 16g). The powder after mixing was pulverized and calcined at 600° C. for 10 hours, and the weight of the powder after cooling was 252.6 g. The volume of the mixed acid solution prepared is 2500mL, wherein the concentration of sulfuric acid is 20%, the concentration of nitric acid is 5%, and the concentration of citric acid is 2%. Heat the mixed acidic solution to 90°C, add the roasted mixed powder, stir and impreg...
Embodiment 3
[0037] 100 g of the 3996 waste hydrogenation catalyst was calcined at 450° C. for 4 hours, and then pulverized to 120 mesh after cooling. 78.0 g was obtained, and the contents of molybdenum and nickel (by weight of oxide) were analyzed to be 23.8% and 4.1%, respectively. Mix with alkaline matter, the weight ratio of sodium carbonate and spent catalyst is 1:1 (weight is about 80g), the weight ratio of sodium bicarbonate and spent catalyst is 0.5:1 (weight is about 40g), the weight ratio of sodium hydroxide and spent catalyst is The weight ratio is 0.1:1 (the weight is about 8g). The powder after mixing was pulverized and calcined at 700° C. for 10 hours, and the weight of the powder after cooling was 191.6 g. The volume of the mixed acid solution prepared is 1900mL, wherein the concentration of sulfuric acid is 15%, the concentration of nitric acid is 3%, and the concentration of citric acid is 1%. Heat the mixed acidic solution to 110°C, add the roasted mixed powder, stir an...
PUM
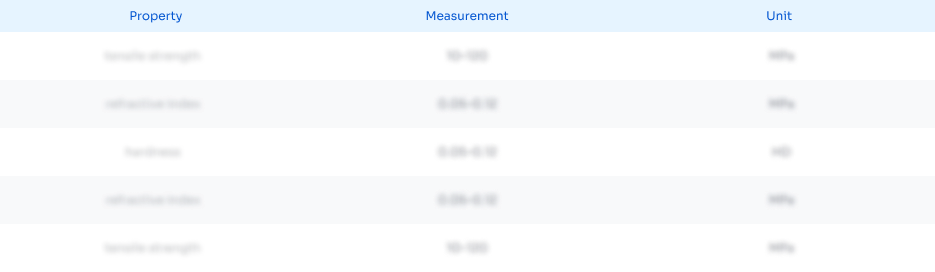
Abstract
Description
Claims
Application Information

- R&D
- Intellectual Property
- Life Sciences
- Materials
- Tech Scout
- Unparalleled Data Quality
- Higher Quality Content
- 60% Fewer Hallucinations
Browse by: Latest US Patents, China's latest patents, Technical Efficacy Thesaurus, Application Domain, Technology Topic, Popular Technical Reports.
© 2025 PatSnap. All rights reserved.Legal|Privacy policy|Modern Slavery Act Transparency Statement|Sitemap|About US| Contact US: help@patsnap.com